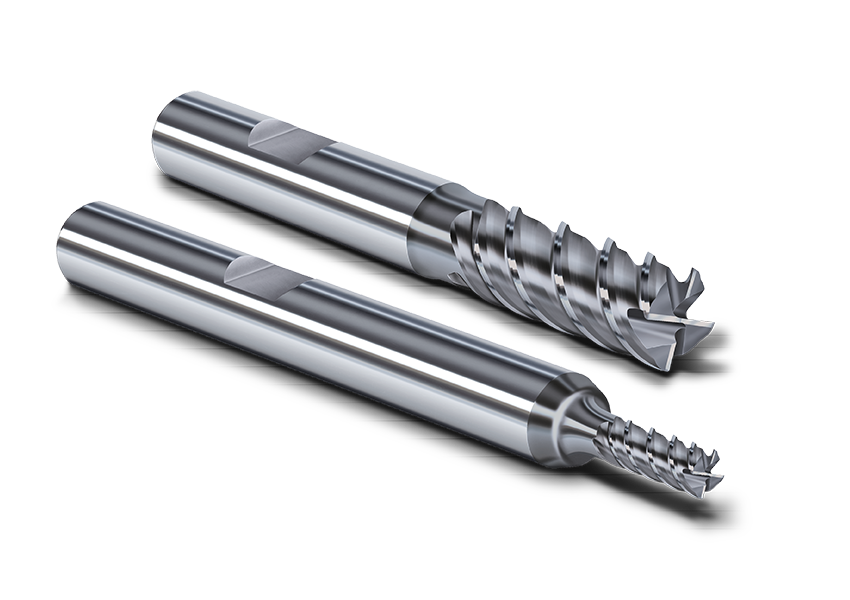
E-Cut – normal length design for minimal burr formation and first-class surface qualities
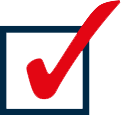
Significantly higher service life for 2.5D machining
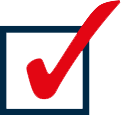
Extremely easy and quiet cutting
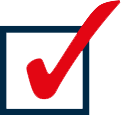
Low burr formation
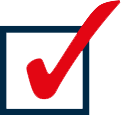
Perfect application data in the FRAISA ToolExpert®
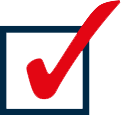
Brilliant surface quality
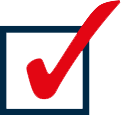
Sustainable service offers with FRAISA ReTool®Services
High-precision finishing cutter for excellent surface qualities
The E-Cut milling cutters in the normal length version have been specially developed for applications where the highest surface quality,
minimal burr and flash formation and optimum dimensional accuracy are required.
The optimized tool geometry and a high-precision ground cutting edge enable virtually burr-free machining even with demanding materials.
The E-Cut milling cutter shows its strengths particularly in precision mechanics - for example in the machining of watch links: The
workpieces have a perfect surface and achieve maximum dimensional accuracy without reworking.
Innovative technologies for maximum precision
The combination of an optimized tool geometry, the hard and very smooth MULTICHROM high-performance coating and
the wear-resistant substrate is the key to the success of the new E-Cut. The high-performance coating reduces
heat generation and tool wear, ensuring consistent performance even at high cutting speeds.
Optimized chip spaces and a precisely tuned rake angle allow chips to be removed smoothly - a major advantage,
especially when machining fine precision components.
Thanks to the use of these innovative technologies, the E-Cut achieves an extremely long tool life and delivers
consistently high quality throughout its entire service life.
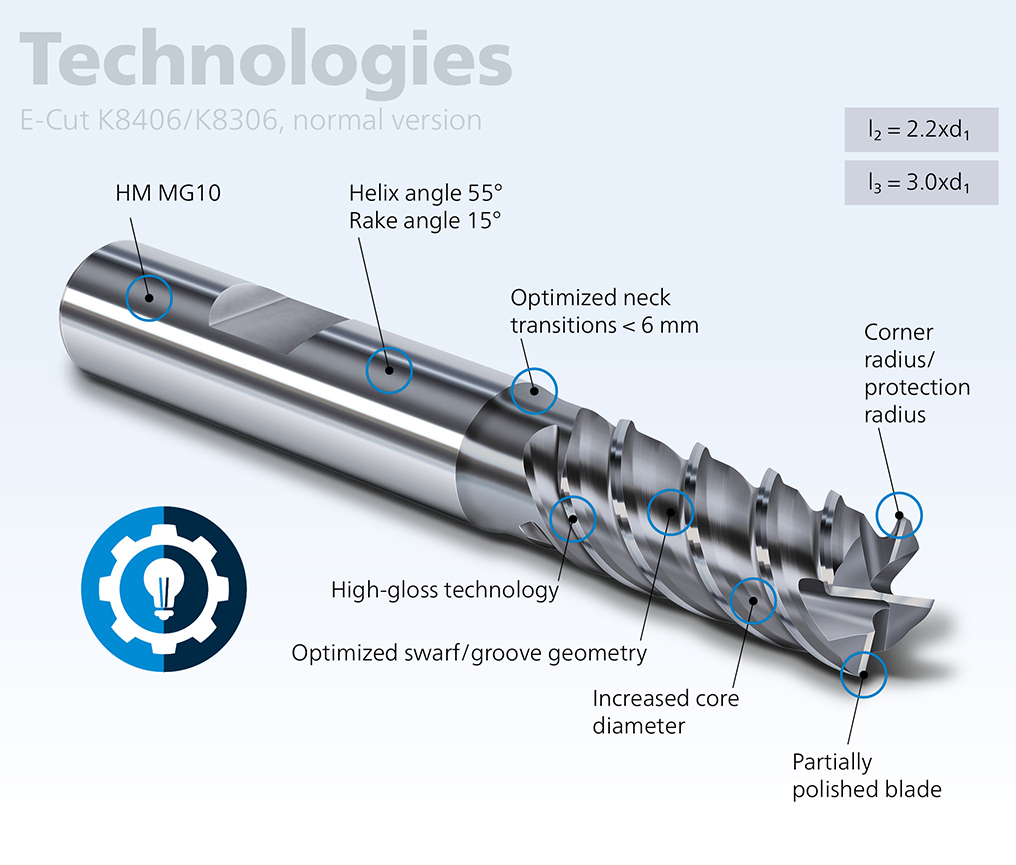
MULTICHROM high-performance coating
Low burr formation due to excellent wear properties
Detailed microscope images prove the minimal tool wear - even after long periods of use. The fine
cutting edge remains intact over the entire tool life, guaranteeing consistently high machining quality.
The images also document the significant reduction in the formation of scalloping: While conventional
milling cutters often leave visible material build-up, the E-Cut with its superior performance achieves
a smooth and even surface even on delicate components.
Workpiece: Inox 316L / 1.4435, after 180 minutes

Workpiece: Inox 316L / 1.4435, after 180 minutes
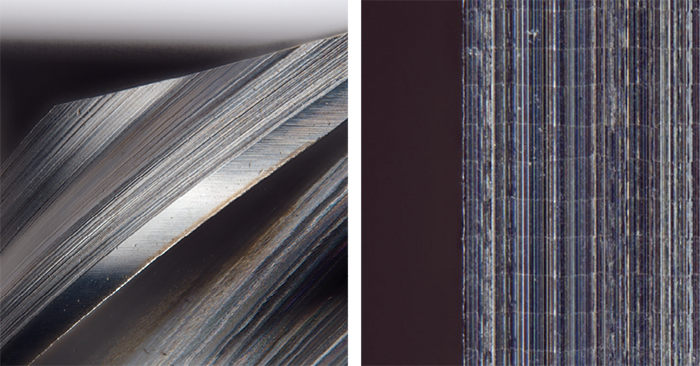
Long service life for 2.5D machining
The new E-Cut tools achieve significantly longer operating times for 2.5D machining than conventional finishing cutters. The following graphic illustrates this impressively:
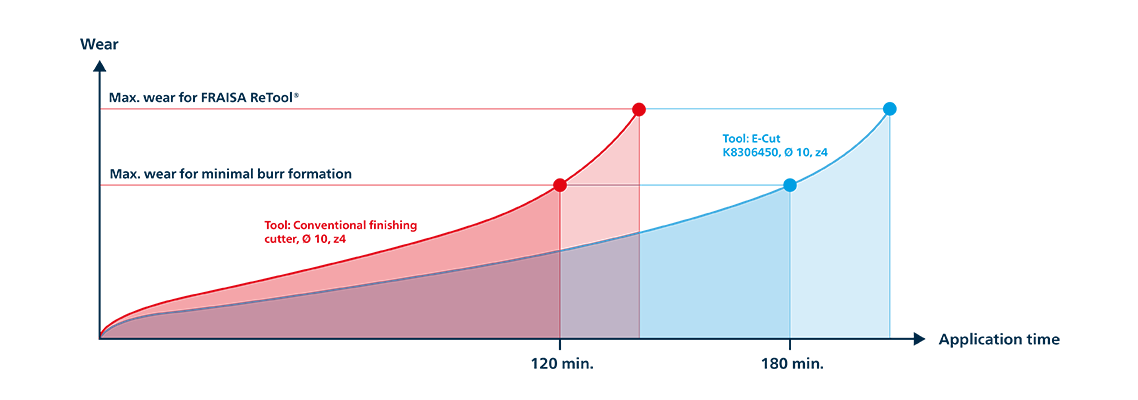
Versatile applications in high-precision industries
Thanks to its innovative design, the E-Cut milling cutter is suitable for a variety of demanding applications:
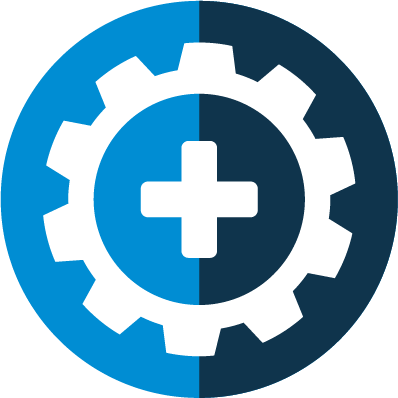
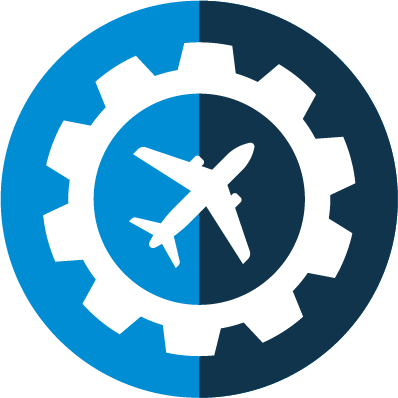
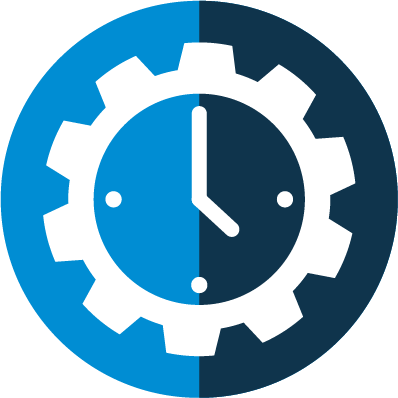
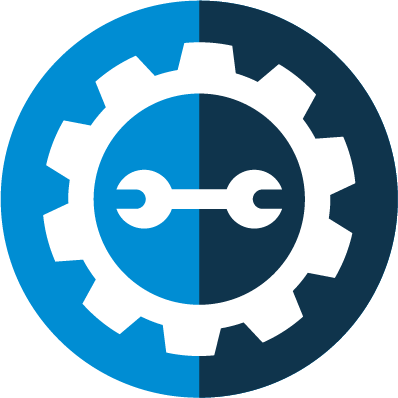
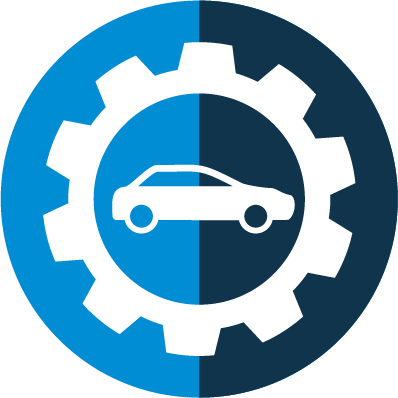
Medical technology – Perfect dimensional accuracy and burr-free surfaces are essential for components such as implants or surgical instruments. The optimized cutting geometry of the E-Cut ensures clean machining without material stresses.
Jewelry and watchmaking technology – In the production of watch links or fine jewelry components, the E-Cut guarantees flawless surfaces without time-consuming reworking. The precise edge guidance prevents material fraying.
Aviation – Wear resistance and material protection are essential requirements for machining in the aviation industry. Here too, the E-Cut impresses with its long tool life and reliable performance on high-strength materials such as titanium, stainless and heat-resistant steels.
Contract manufacturing and general mechanical engineering – A high degree of universality with regard to different materials is of great importance in contract manufacturing. The E-Cut can be used very universally for pre-finish and finish applications and HPC up to 0.15xd. The corresponding cutting data is available in FRAISA ToolExpert®.
Mold making and automotive – When machining molds or automotive components in mostly tempered, stainless and alloyed steels, perfect surface finishes and low burr/burr formation are very important.
Our other E-Cut products
You might also be interested in
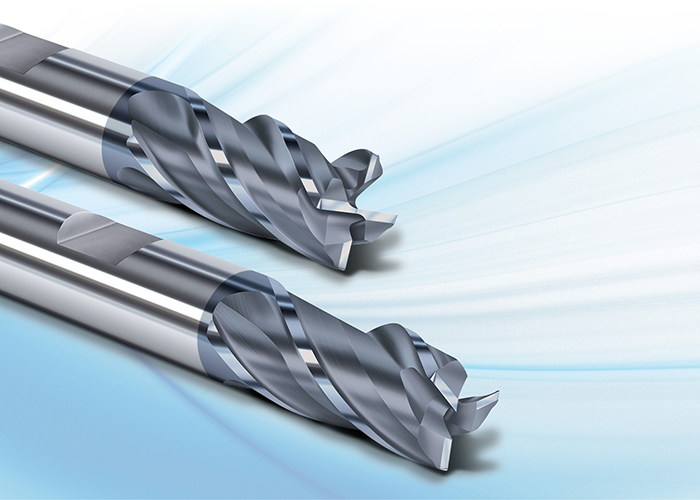
E-Cut - short length design for high tool stability thanks to short cutting edge
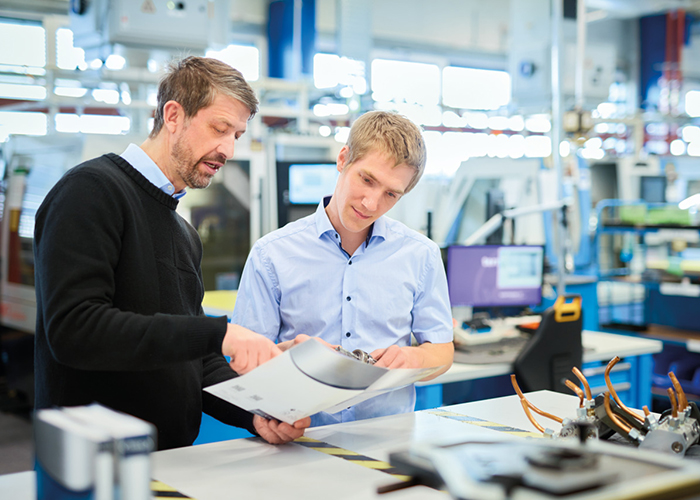
Personal application advice and optimum cutting data in FRAISA ToolExpert®