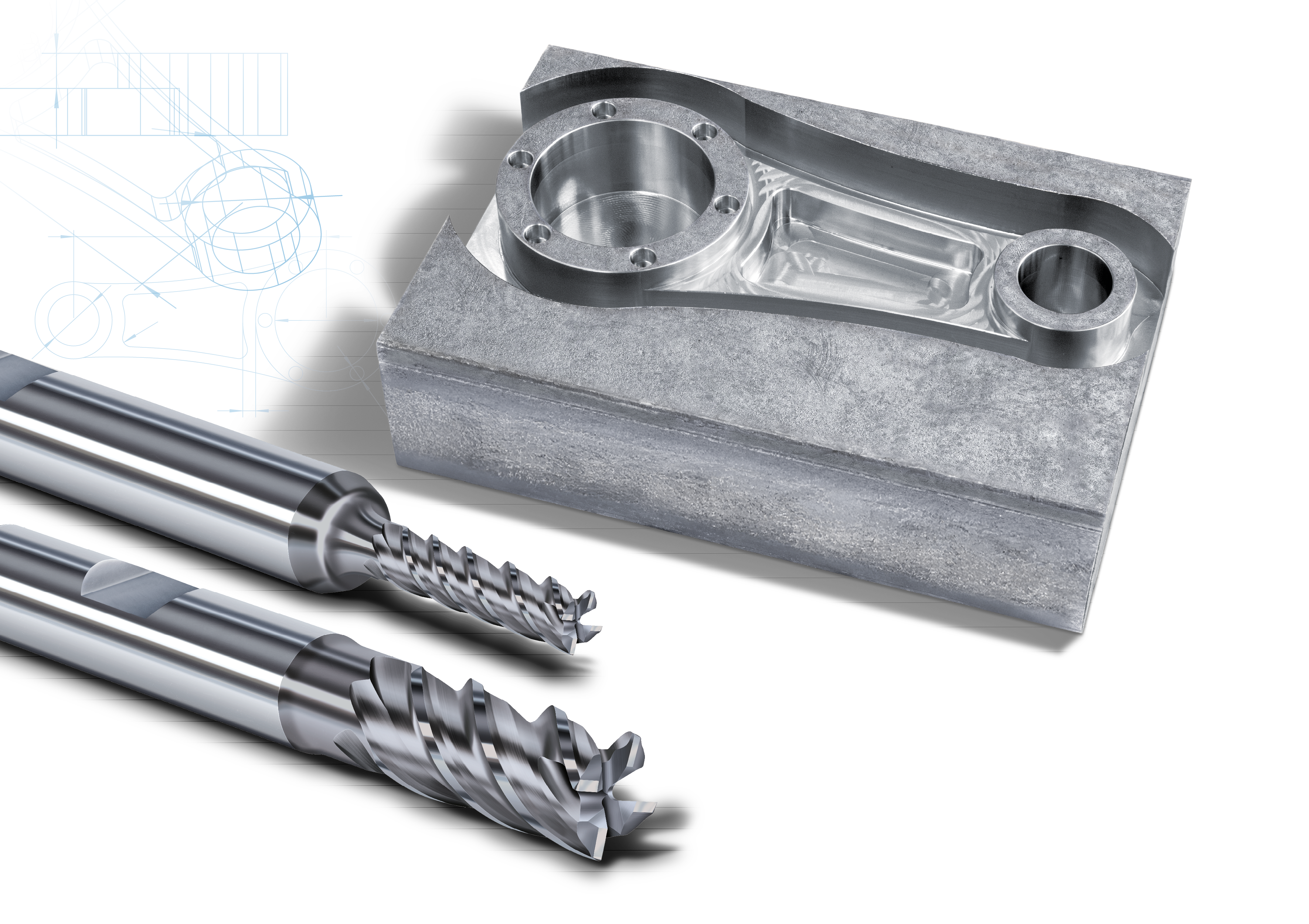
FRAISA SteelCut – Process-safe milling of soft steel at the highest level
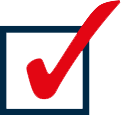
Universal application for maximum productivity
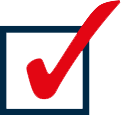
Valuable application knowledge in the area of «steel < 850 N/mm2 (HRC < 24)»
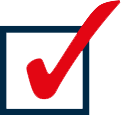
Reproducibility, repeatability and reliability
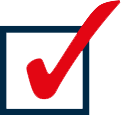
Consistent product range with constant l/d ratios
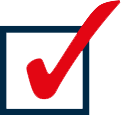
Excellent wear properties, long service life and high process reliability
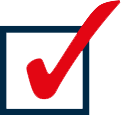
Diameter range 3 mm to 20 mm, with or without side clamping flat surface
Challenges when milling mild steel
Whether mild steel, quality steel or heat-treated steel - the many types of mostly unalloyed
or low-alloy materials are demanding and difficult to machine. They have a ductile and at the
same time inhomogeneous microstructure and generate unpredictable wear during machining.
The materials are usually formed, joined or reworked by forging. As a result, the residual stresses
are not evenly distributed, which poses an additional challenge during machining. The areas of structural
steel, unalloyed quality steel, heat-resistant steel, unalloyed engineering steel and fine-grained structural
steel alone already comprise 150 different materials.
FRAISA has developed the new SteelCut milling system with a very broad material coverage and robust
behavioral characteristics in order to be able to machine mild steel reliably and efficiently. Depending
on the material, there are different requirements within the same machining class - many tools can only
cover a very small range of applications in the material class Rm < 850 N/mm2. This is precisely where
the SteelCut proves its strengths by opening up completely new application horizons.
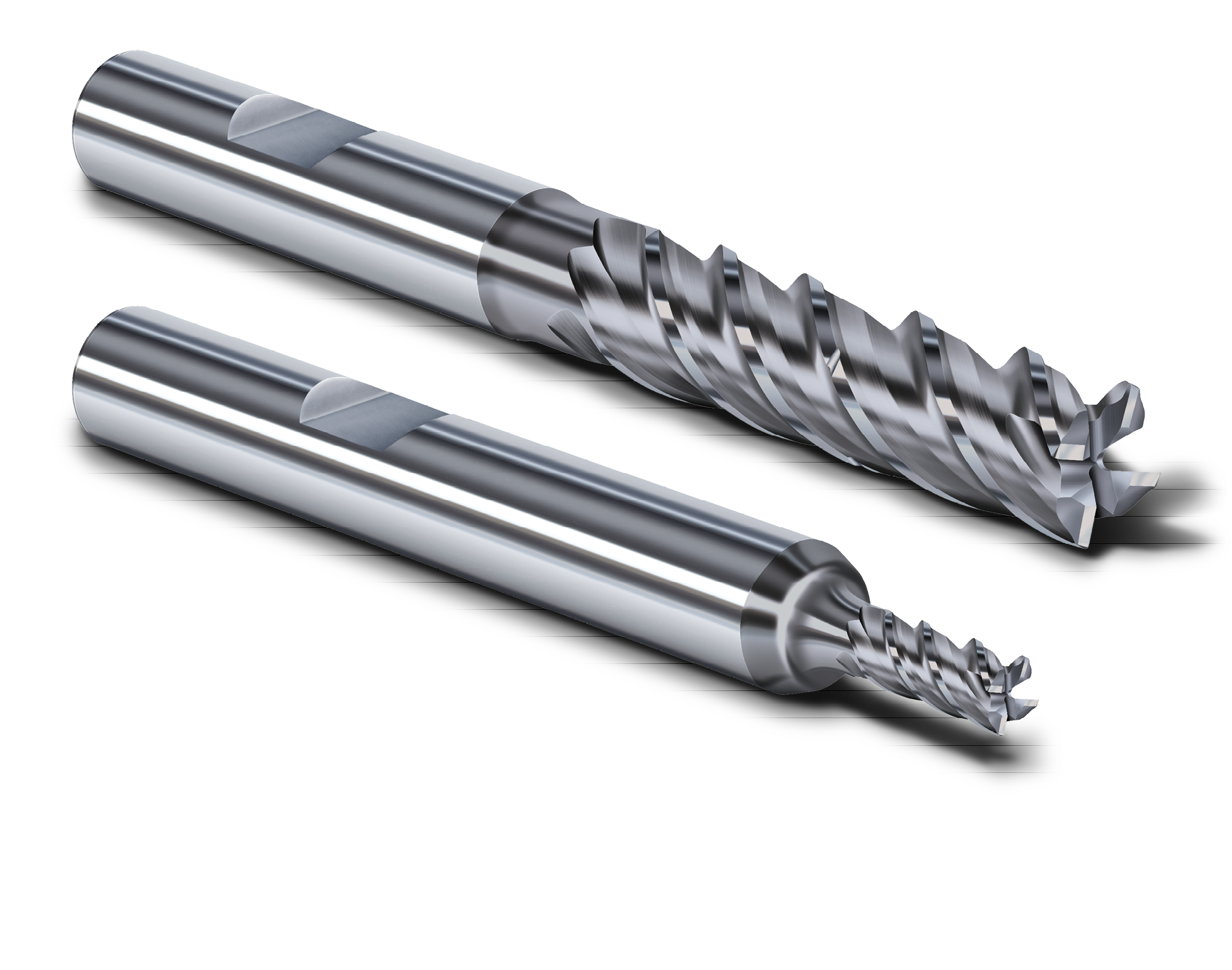
Not all mild steels are the same
Within the mild steel material group, structural steel St-52 / 1.0570 and heat-treated steel 42CrMo4 / 1.7225, for example, exhibit completely different wear behavior in wet machining (emulsion) with the same application data. The task for the FRAISA engineers was to develop a consistently efficient system that could master the following challenges when milling mild steel:
Formation of built-up edges:
Due to the low hardness of mild steel, material can build up on the cutting edge,
which can lead to poor surface quality and tool wear.
Solution: The use of coated tools and high cutting speeds.
Chip removal:
Mild steel tends to produce long, cohesive chips that can block the milling path.
Solution: Optimization of the tool geometry for optimum chip formation and chip evacuation.
Heat generation:
High cutting speeds can lead to excessive heating of the workpiece and the tool, which can cause dimensional inaccuracies.
Solution: The correct choice of cutting parameters, e.g. from the FRAISA ToolExpert®.
Oscillations (vibrations):
Long tool overhangs can cause vibrations, which can lead to poor dimensional accuracy and tool wear.
Solution: More stable clamping, smaller infeeds and the use of milling cutters with variable cutting edge spacing.
The SteelCut milling system was specially developed for machining soft steels and scores with
excellent tool life, high process reliability combined with silky-smooth running and optimum
chip evacuation. The SteelCut unfolds its full potential in both dry and wet machining with
emulsion or oil and delivers outstanding results.
The newly developed hard and very smooth MULTICHROM high-performance coating has a positive
effect on service life and guarantees an increased metal removal rate during milling and plunging.
The high-performance milling cutters can be used universally and cover both HPC and HDC processes.
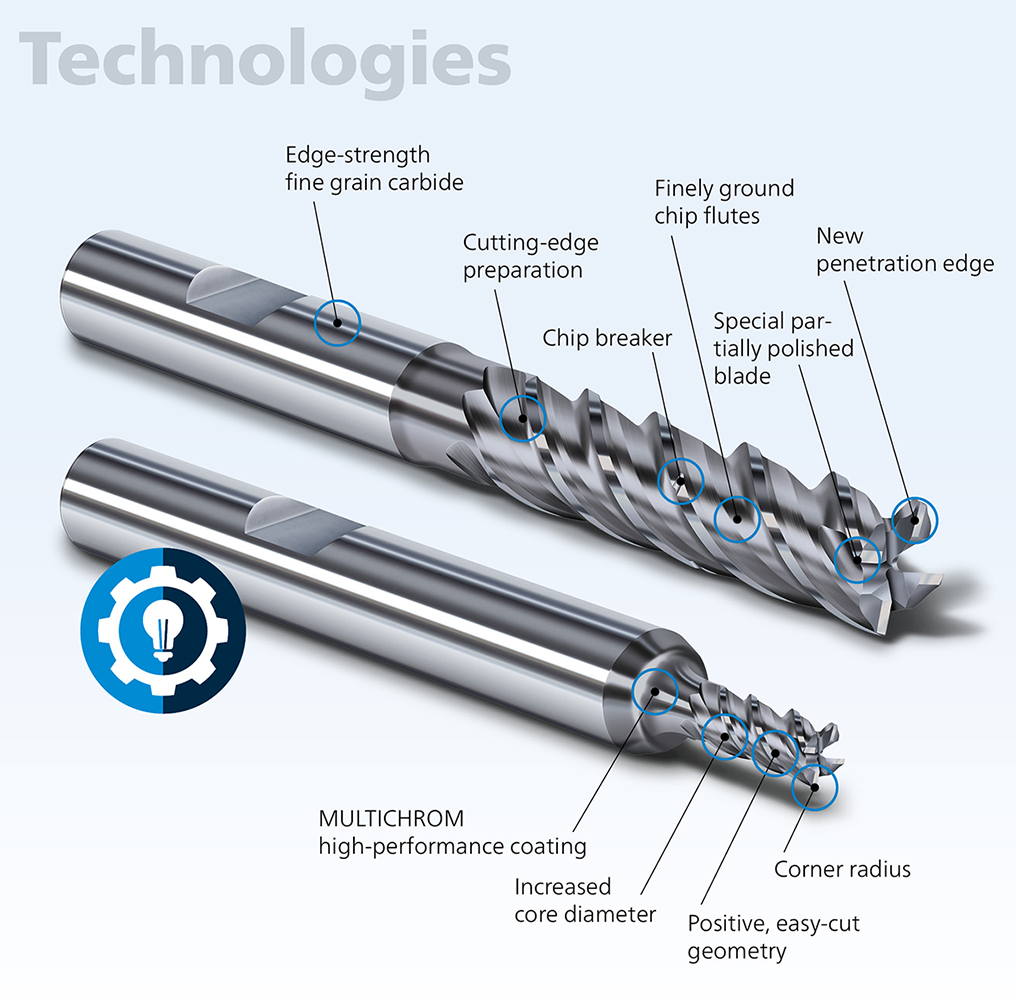
- Edge-resistant ultra-fine grain carbide for plunge, HPC, HDC and finish machining and long tool life
- High-performance MULTICHROM coating for maximum process reliability and low material adhesion
- Low sticking tendency, prevention of adhesion and built-up edge formation
- High wear resistance even under high thermal loads
- High-precision coating thickness distribution, maximum tool precision
- Chip breaker system for better chip evacuation
- Positive rake angle for a soft, light cut to prevent chips from jamming
- Tooth grinding reduces cutting forces, improves chip evacuation and reduces tool wear
- Plunge face enables smooth and low-vibration plunging
- Corner radius for better tool life and surface quality
SteelCut - the reliable all-rounder for maximum performance and tool life
FRAISA carries out extensive tests in order to keep an eye on the state of tool and application
technology at all times. The tools are tested in different materials with various milling strategies.
The focus was on HPC milling, plunging and HDC milling, as these involve particularly high mechanical
and thermal loads. These tests ensure that the tools cover a wide range of materials and applications
while guaranteeing maximum performance and service life.
The following wear images are impressive proof of this:
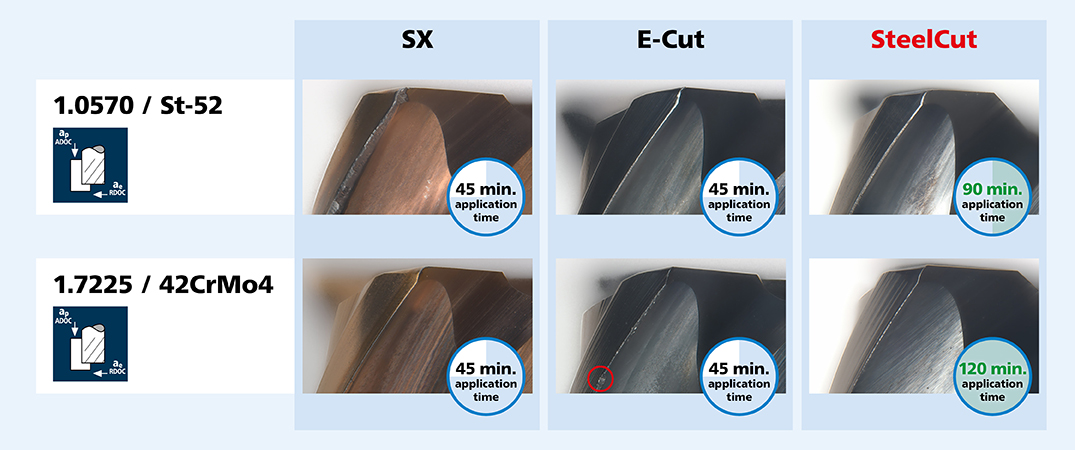
Advantages of the SteelCut milling system:
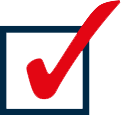
Perfect for plunging, HPC, HDC and finishing
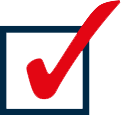
Broad application and material range
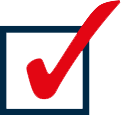
Optimal chip formation and good chip removal
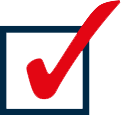
Perfect application data in the FRAISA ToolExpert®
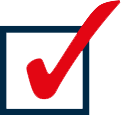
High tool stability and resistance
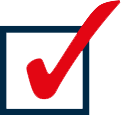
Sustainable service offers with FRAISA ReTool®Services
Application advice and optimum cutting data for mild steel milling
In addition to the SteelCut milling tools, FRAISA also provides valuable application knowledge for correct machining. FRAISA application engineers advise our customers on all questions relating to the next machining challenge, e.g:
- What is the optimum cutting speed to avoid built-up edge formation, for example?
- What feed rate should I choose per tooth?
- What are the radial and axial infeeds for reliable machining?
- Which application is best suited?
- What are the process costs (e.g. tool and machine costs)? How can these be optimized, e.g. by using FRAISA ReTool®?
The result is high-precision application parameters that are bundled in the FRAISA ToolExpert® online cutting data calculator and can be called up quickly and easily at any time. The integration of online interfaces also enables direct import into the CAM or TDM system - compared to manual input, this significantly reduces the time required and susceptibility to errors.
Now new in FRAISA ToolExpert®:
Performance data to reduce overall machining costs
For the HPC lateral roughing (partial cut) and HPC grooving (full cut) applications, you can now choose between two differently designed cutting data sets (applies to all SteelCut tools from a diameter of 6 mm):
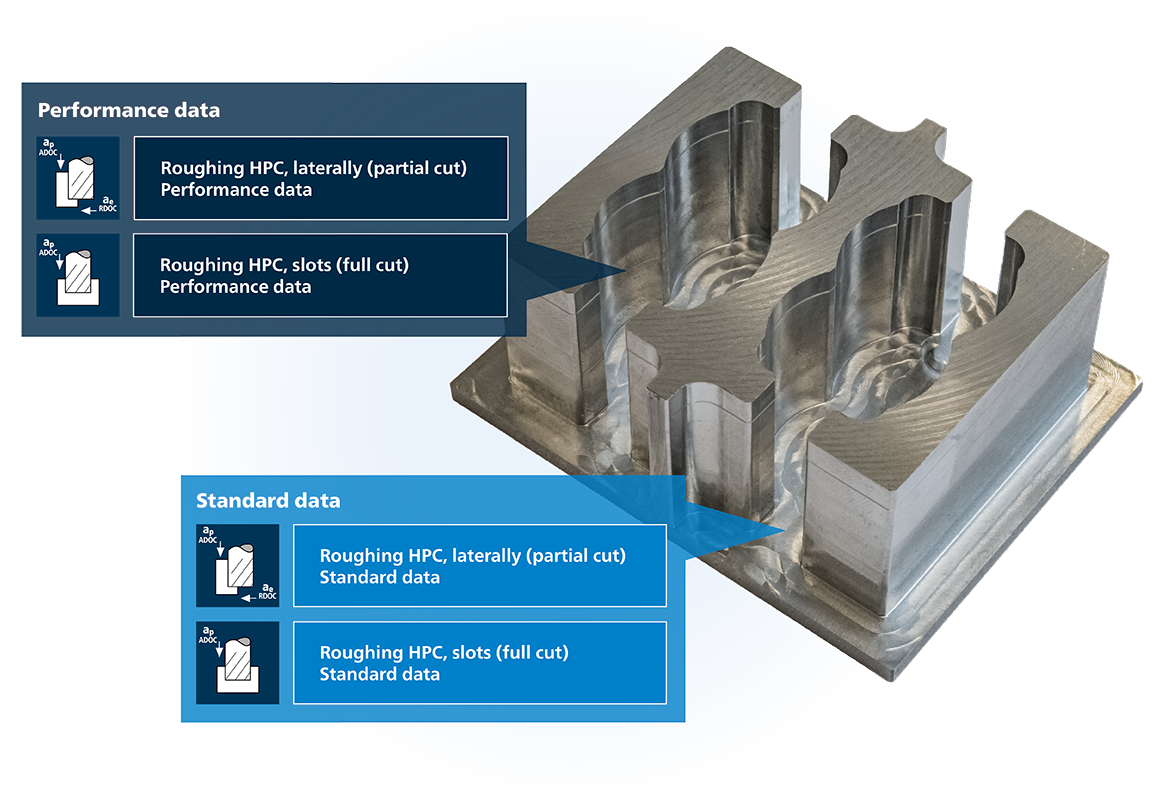
The standard data focuses on increasing process reliability and optimized tool life. The performance
data focuses on reducing overall machining costs and optimizing productivity.
The following graphics illustrate the impressive increase in productivity that can be achieved with the performance data:
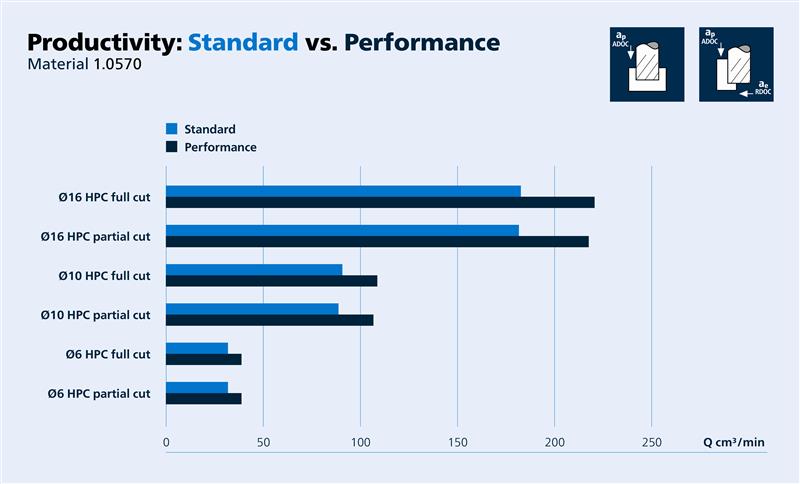
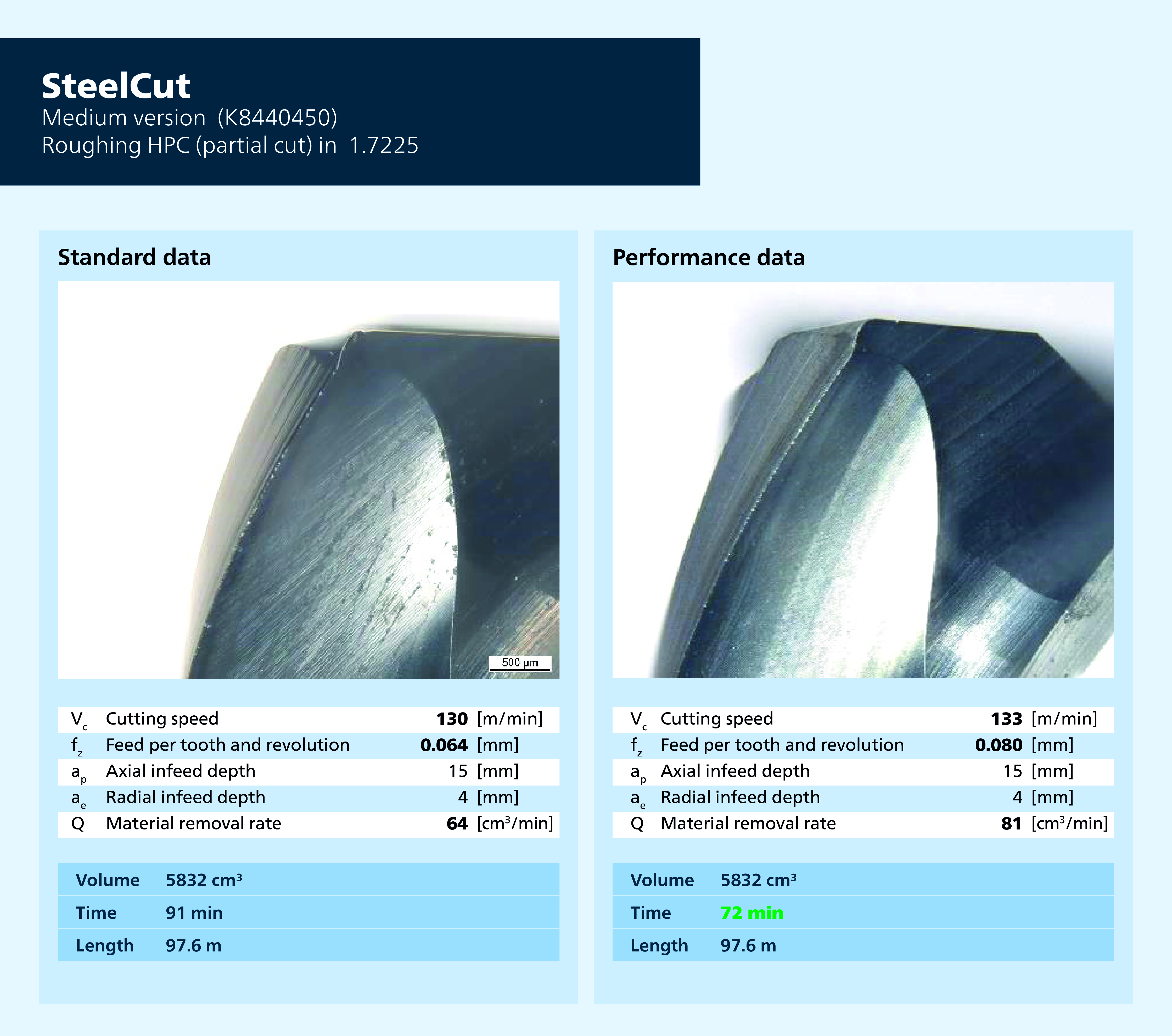
Whether you want to increase your process reliability with optimum tool life or reduce your machining costs with optimized productivity - the FRAISA ToolExpert provides you with optimum cutting data for every task. Try it out now - our FRAISA application engineers will be happy to answer any questions you may have.
The FRAISA ToolExpert® advantages at a glance:
Precise: calculation of perfectly coordinated, tool- and material-specific cutting data
Easy: mobile access of data online, at any time, without downloading software
Fast: find application parameters without registration, with just a few clicks
Ordering function: order selected tools via link directly in the webshop
Flexible: optionally search for tools or materials to be processed
Comprehensive: retrieve cutting data for FRAISA tools from a database with more than 11,000 materials
User-friendly: navigate intuitively with a new, responsive design
Safe: import cutting data directly by integrating an XML or JSON interface
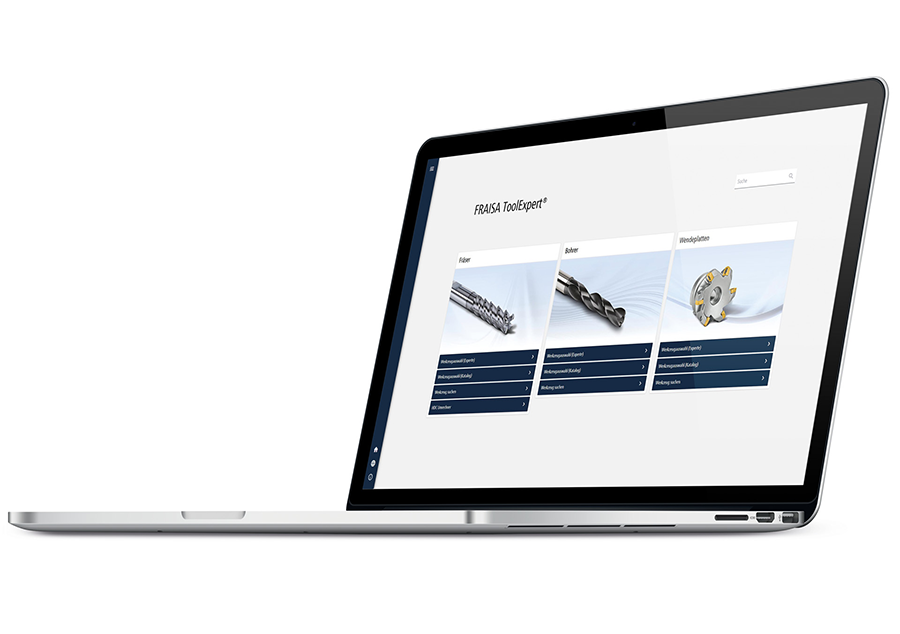
SteelCut - Research and development at the highest level
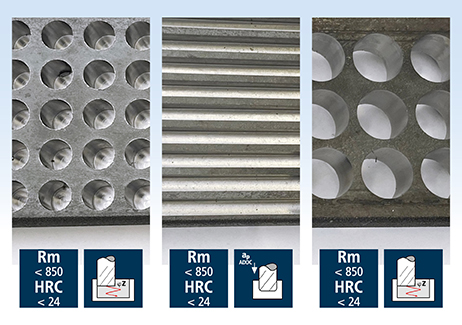
The new SteelCut milling system was developed over two years with around 80 prototypes across all diameters, lengths, layers and technologies. Production standardization, pre-validation and first lot validation, FRAISA ReTool® validation and technology transfer to special tool production ensure reproducible quality. This is of particular importance for the user so that the performance level for automation and processing can be guaranteed at all times.