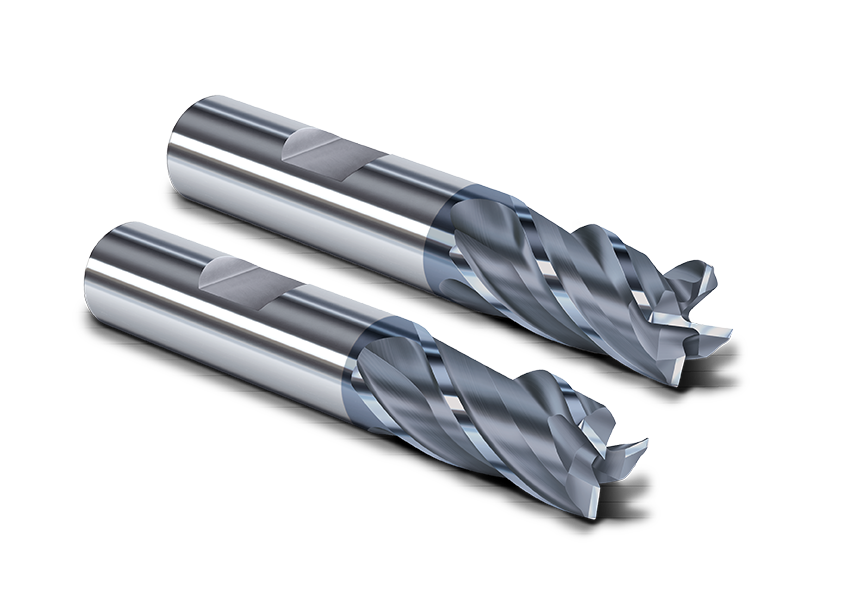
E-Cut - short length design for high tool stability thanks to short cutting edge
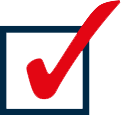
Significantly higher performance for 2.5D machining
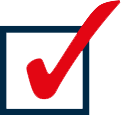
Excellent chip removal for narrow grooves
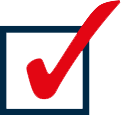
Increased process reliability due to decreased vibration
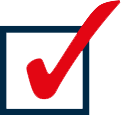
Perfect application data in the FRAISA ToolExpert®
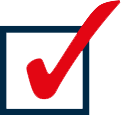
High tool stability due to a short cutting edge
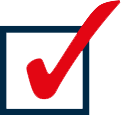
Sustainable service offers with FRAISA ReTool®Services
Highest precision and performance for versatile applications
Our innovative E-Cut milling cutters have been specially developed in the short length version for the best component quality and easy handling. They set new standards in the machining of a wide range of materials and combine maximum precision with maximum performance. The E-Cut achieves excellent results, particularly with materials with a strength of < 850 to 1300-1500 N/mm², stainless steels (Inox) and tool steels (ToolSteel) - often without time-consuming reworking.
Technological advantages for maximum performance
High-precision machining with the E-Cut milling cutters minimizes tolerances in production, resulting in improved accuracy of fit and durability of the end products. Reduced reworking not only saves time and costs, but also increases production efficiency.
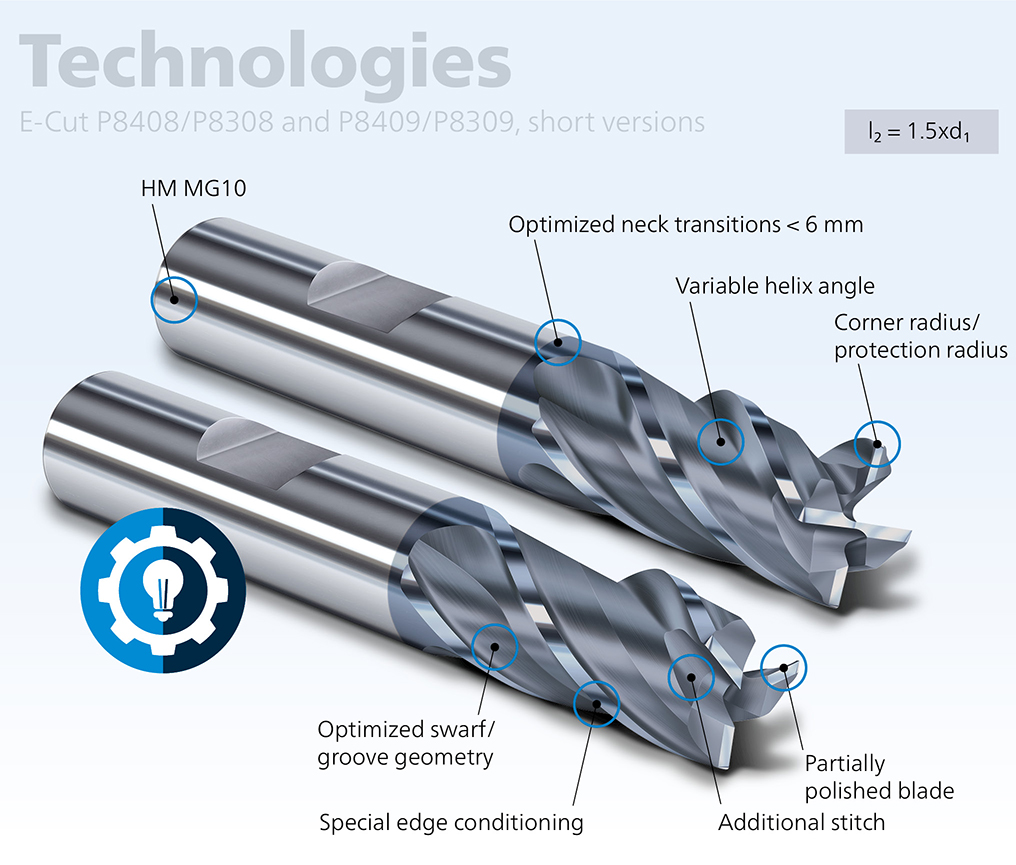
Our E-Cut milling cutters in the short version impress with:
Optimized geometry for reduced cutting forces, improved chip removal and higher feed rates
High-quality coating for minimized wear and improved tool life
Perfect cutting edge stability for reduced vibrations and increased process reliability
Flexible tooth profile for efficient grooving
Efficient chip evacuation and high stability for optimum machining
Efficient chip evacuation prevents clogging of the milling cutter, reduces the thermal load and
enables a consistently high surface quality. This is particularly important for deep grooves or
difficult-to-cut materials in order to avoid tool wear and machine downtime. The high stability
of the E-Cut reduces vibrations and increases process reliability, which leads to more precise
machining results, a longer tool life and a better surface quality of the workpieces. This is a
decisive advantage, particularly in series production and for high-precision components.
The following graphics show the excellent wear properties of the new E-Cut milling cutters:
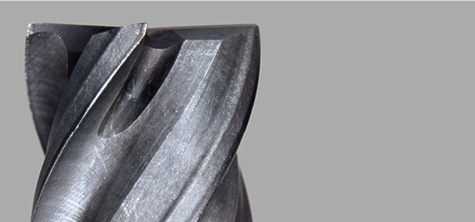
Ø 10, z4
material: Inox AISI
304 / 1.4301, after 65
minutes
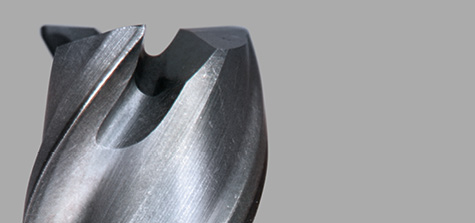
Ø 10, z3
material: Inox AISI
304 / 1.4301, after 65
minutes
Consistently high machining quality ensures that components always meet the high requirements of the industry. This is particularly important in sectors with strict quality standards, such as medical technology or aviation. High repeat accuracy also saves material costs and reduces waste.
E-Cut - the ideal solution for many industries
Contract manufacturing – high efficiency and long tool life for cost-effective machining
Mold making – precise results for complex geometries with minimal reworking
General mechanical engineering – versatile use in a wide range of applications
Automotive – perfect surfaces for sophisticated components, crucial for precision components
Aerospace – stable performance even with high-performance materials and safety-critical components
Medical technology – maximum precision for sensitive components with strict quality requirements
Watch industry – fine structures with extremely little reworking, precise micromachining
Tool and mold making – consistently high machining quality for complex and demanding molds
Our other E-Cut products
You might also be interested in
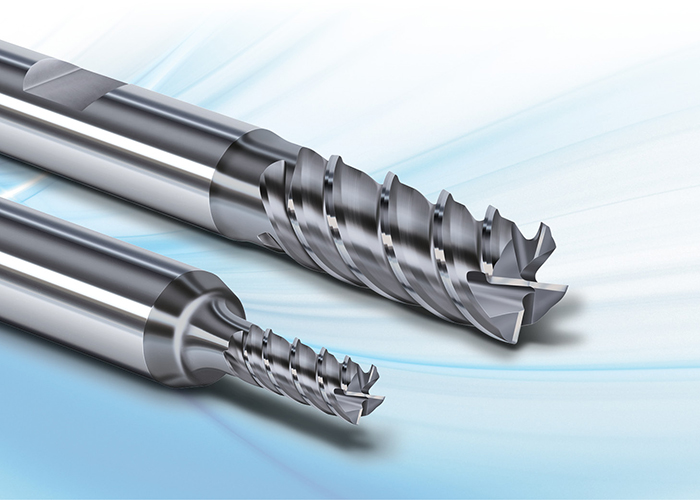
E-Cut - normal length design for minimal burr formation and first-class surface qualities
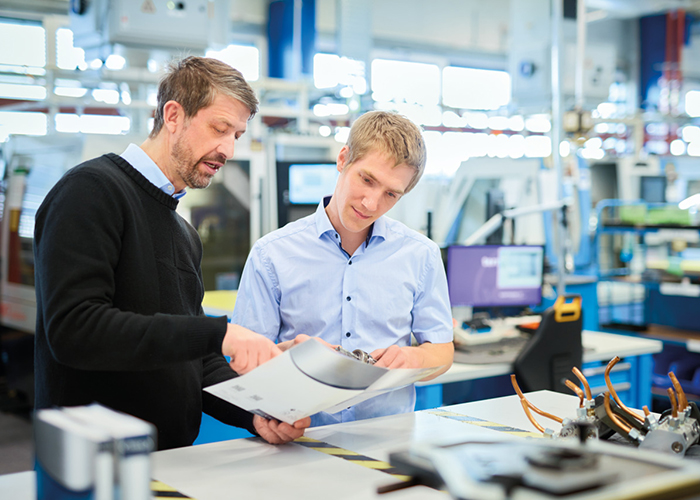
Personal application consultation and optimum cutting data in FRAISA ToolExpert®