We would be happy to support you with your next machining challenge. Simply make an appointment for a free application consultation:
Arrange a free application consultation!
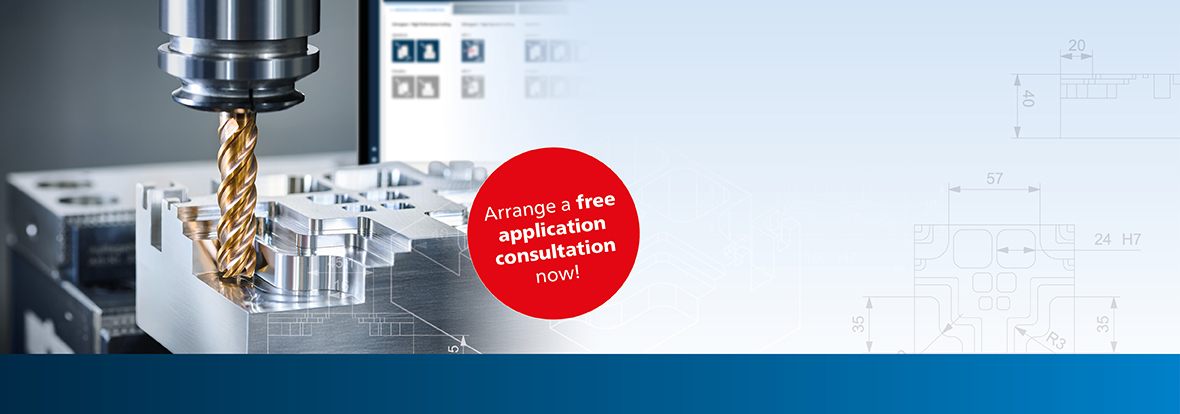
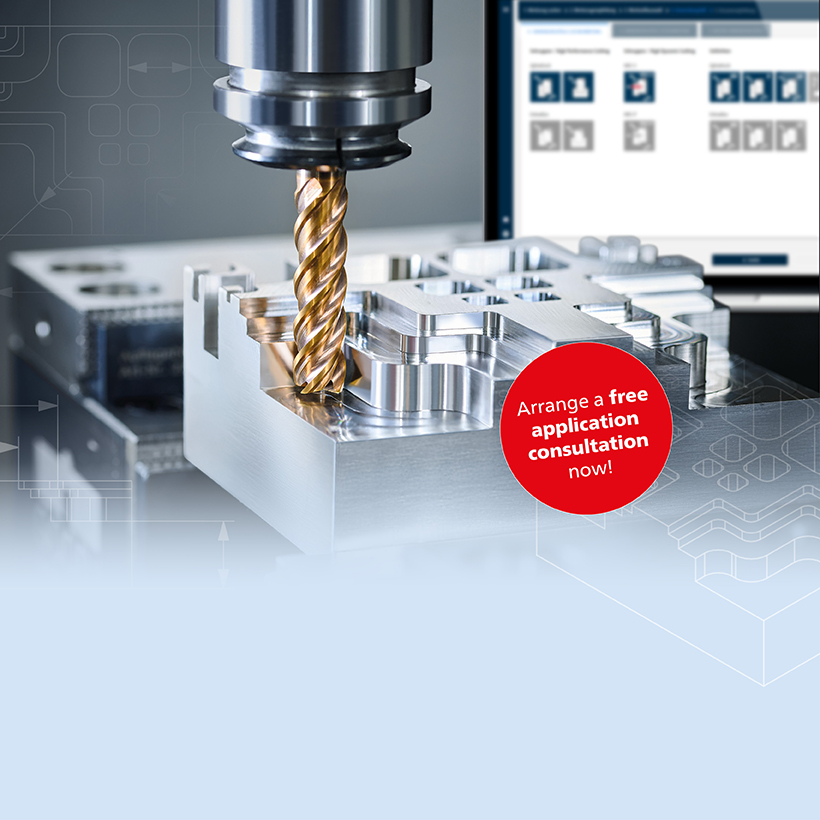
FRAISA ToolExpert® - Optimal cutting data for maximum process reliability
We would be happy to support you with your next machining challenge. Simply make an appointment for a free application consultation:
Arrange a free application consultation!
Efficient milling and drilling with the FRAISA ToolExpert® speeds and feeds calculator
In modern machining technology, precise cutting data is crucial for successful and efficient machining. This is especially true in autonomous processes that run for hours without human process monitoring, where reliable cutting data is essential. With FRAISA ToolExpert, you can not only optimize your processes - whether milling, drilling or machining with indexable inserts - but also make them reliable with little effort.
The speeds and feeds calculator quickly and reliably determines the right cutting data for your material, your tool and your application - including for autonomous production. It provides you with detailed recommendations on cutting speed, rotational speed and speeds and feeds milling, among other things, which are precisely tailored to your requirements.
FRAISA ToolExpert helps you to find the best settings for CNC milling and drilling, in order to maximize the service life of your tools. From the selection of the right milling tools and drills to the correct use of indexable inserts, FRAISA ToolExpert offers you everything you need for efficient machining.
With FRAISA ToolExpert, you can make your machining processes more efficient and benefit from the precise recommendations of this powerful tool.
We would be happy to support you with your next machining challenge. Simply make an appointment for a free application consultation:
Arrange a free application consultation!
Table of contents:
Brief introduction to the FRAISA ToolExpert®: speeds and feeds calculator: What can it do?
The most important functions of the ToolExpert speeds and feeds calculator at a glance
Time savings thanks to quick and easy user interfaces
Advantages of using the speeds and feeds calculator
Integration of ToolExpert into the CAM programming process
FAQ: Frequently asked questions and answers
Start ToolExpert®
Arrange a free application consultation!
Brief introduction to the FRAISA ToolExpert® speeds and feeds calculator: What can it do?
FRAISA ToolExpert is your digital tool for precise cutting data. The tool is an indispensable aid for anyone who works with FRAISA cutting tools and needs precise cutting data quickly. Thanks to this innovative online tool, the time-consuming manual calculation of rotational speed or speeds and feeds milling is a thing of the past. With just a few clicks, you can determine the optimum parameters for your cutting process - regardless of whether you use conventional or CNC technology.
ToolExpert provides you with over two million cutting data that are specifically tailored to tools and materials. It is possible to not only call up the appropriate data for a single tool, but to also plan complex machining operations by combining different tools and applications. The data can be conveniently downloaded as PDF, DXF or XML files.
FRAISA invests a large proportion of its total development costs in the preparation of this tool- and material-specific cutting data, which is tested under real conditions in our application centers. The result is high-precision application parameters that can be called up at any time to raise your productivity to a new level.
FRAISA ToolExpert not only provides you with the best cutting data but also allows you to download CAD data and order the right tool directly from the webshop. This equips you for efficient and successful production in an increasingly digitalized world.
The most important functions of the ToolExpert speeds and feeds calculator at a glance
FRAISA ToolExpert is a comprehensive solution for optimizing your cutting processes. The tool offers a wide range of functions that make it easier for you to select the right tool, determine precise cutting data and plan complex machining operations.
The extensive material database enables you to select the right material for your application quickly and efficiently. It does not matter whether it is aluminum, steel, plastics or difficult-to-machine alloys with nickel, ToolExpert offers the right cutting tool and precise cutting data recommendations for every material. The tool provides exact data on speeds and feeds milling, speed, cutting speed and other key parameters, regardless of whether you are milling or drilling.
ToolExpert also offers support for CAM projects by providing free CAD 3D models as DXF and XML files. These simplify the planning and implementation of projects considerably. If you need to combine different applications and tools, we will of course also provide you with the relevant data and recommendations.
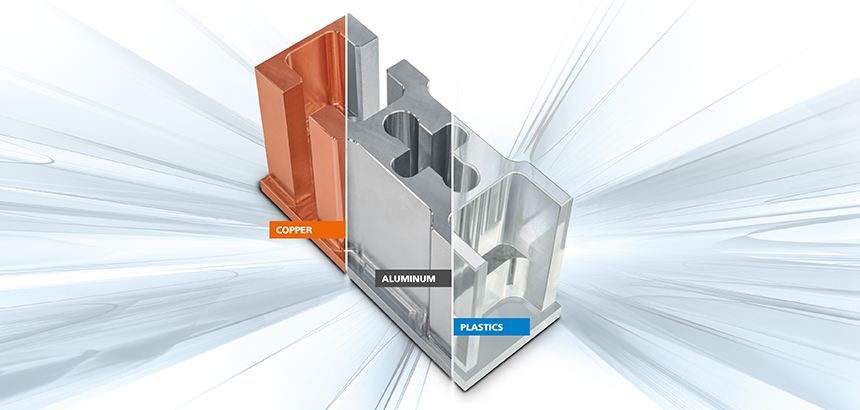
1
1. material selection:
With access to an extensive material database, you can easily search for specific materials. ToolExpert makes it easy for you to search for the right material, whether by material number, DIN or other criteria.
Would you like to mill aluminum, machine plastics, drill steel or process nickel? Of course: In ToolExpert you will find the right cutting tool and cutting data recommendations for around 11.000 materials.
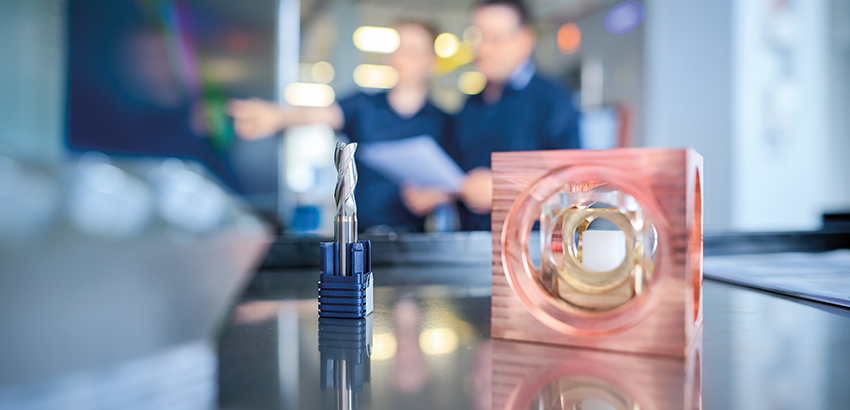
2
2. tool selection:
The selection of the appropriate FRAISA tool depends largely on the respective application. Please consider the material you are machining and the requirements for precision and surface quality.
FRAISA offers you a wide range of milling tools that have been specially developed for different applications. This ensures that your work always delivers first-class results, whether it is CNC milling or conventional milling. You can also count on reliable data for your FRAISA drills and indexable inserts.
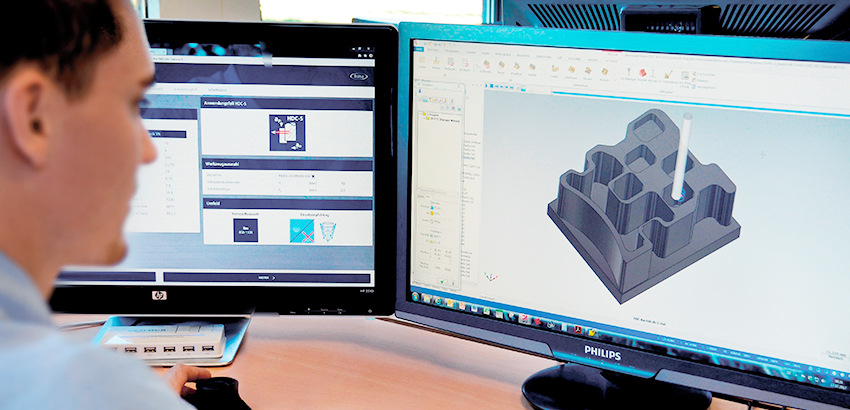
3
3. cutting data recommendations:
FRAISA ToolExpert offers you comprehensive cutting data recommendations that are specifically tailored to your milling and drilling requirements. The tool provides precise information on important parameters for milling, including cutting edge diameter, number of cutting edges, cutting speed, tooth feed and axial and radial infeed depth of cut.
The tool also enables speeds and feeds to be determined quickly and easily. ToolExpert also provides detailed data for drilling, such as recommendations on cutting diameter, cutting speed, feed per revolution, and rotational speed. It also provides information on the drilling depth, the maximum drilling depth and the time required per hole in order to make the entire machining process as efficient as possible.
ToolExpert also offers comprehensive support for your CAM projects. We provide you with free CAD 3D models as DXF and XML files to make it easier for you to plan and implement your projects. The CAD data provides you with the right information at all times, making your work more flexible and efficient.
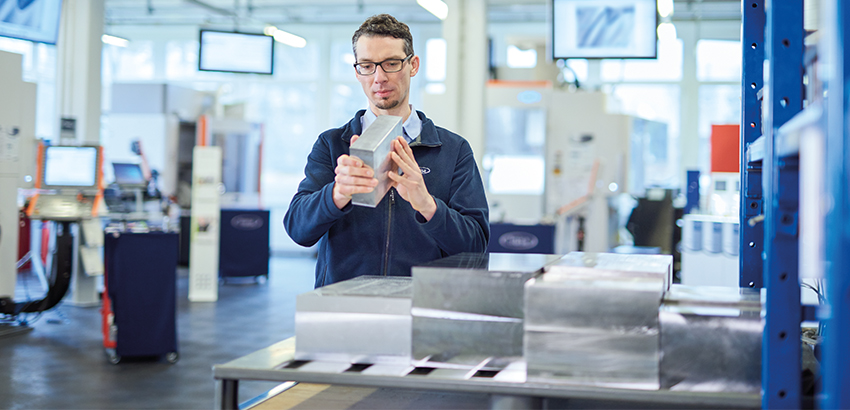
4
4. combine use cases, tools and materials:
Would you like to combine different use cases and tools for machining your workpiece? With FRAISA ToolExpert, you can easily combine all use cases and tools for machining your workpiece.
For example, you have chosen a suitable tool for trochoidal milling in aluminum (High Dynamic Cutting) with which you can rough walls. In the next step, you can add on data for plunging (High Performance Cutting) and then, perhaps, additional data for other applications such as 2.5D pre-finishing, grooving and finishing. The appropriate tools are suggested for each application.
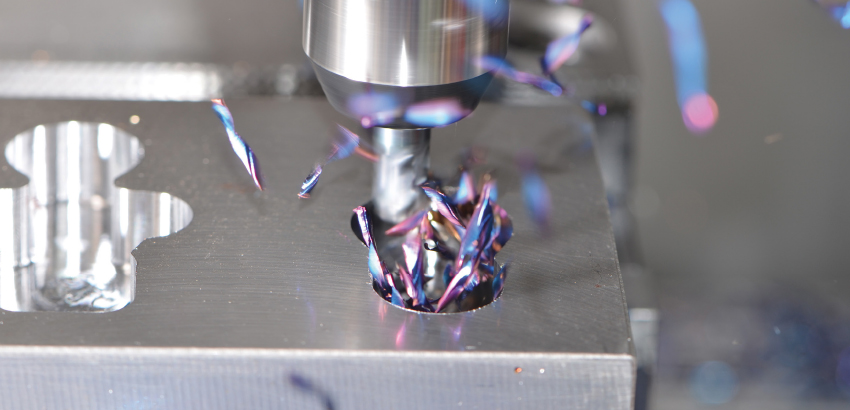
5
5. HDC converter (trochoidal milling)
It is also possible to convert your HPC (High Performance Cutting) cutting data into HDC (High Dynamic Cutting) data.
ToolExpert also offers you the right solutions for complex requirements and CAM projects. We are on hand to advise you on complex issues.

In addition to comprehensive digital support, we are always available for personal and needs-oriented advice. Our technical application consultants will be happy to assist you with questions about the tools and develop tailor-made solutions for process optimization - even for complex machining tasks.
Benefit from the tips and tricks of our experts for your specific machining requirements:
Save time thanks to quick and easy user interfaces
The user interface of the ToolExpert speeds and feeds calculator: How to find your way around quickly
FRAISA ToolExpert impresses with its user-friendly and intuitive interface, which makes it quick and easy to determine the right tools and optimum cutting data for your application.
To make it easier for you to get started, first select one of the three main categories: you can choose between milling tools, drills or inserts. As soon as you have decided on a category, you can adapt the respective tool and the corresponding cutting data to your requirements.
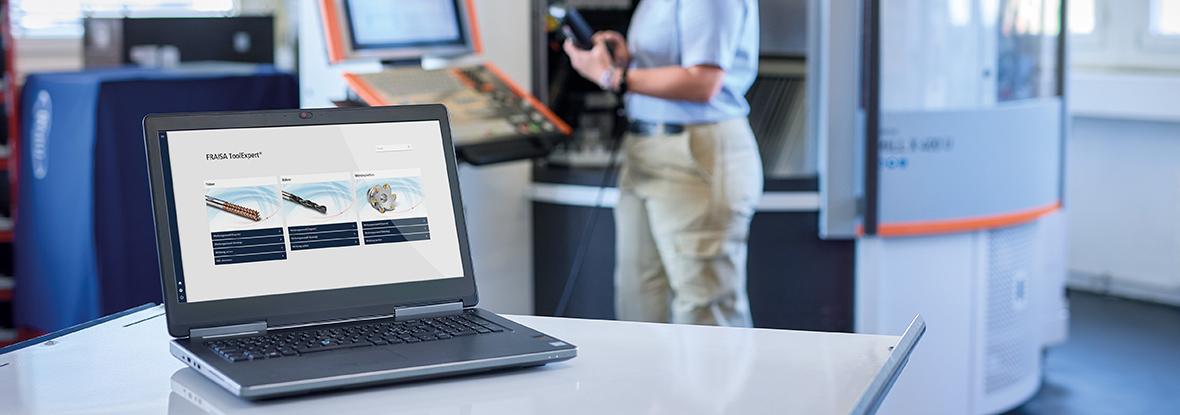
Milling tools: If you select the “Milling tools” category, you can choose from different types of milling tools for every type of machining. ToolExpert offers a wide range of variants, including end mills, corner mills, slot mills and solid carbide milling tools. Micro end mills and copy end mills (ball nose end mills, radius end mills, torus end mills) are also available. This means you can always find the right tool for your specific task. Thanks to the clear structure, you can quickly find the right milling tool, be it with a 6 mm, 8 mm or 12 mm shank.
The ToolExpert suggests suitable milling tools for metal for carbide machining, but also for machining soft non-ferrous metals such as copper and aluminum. You will also find milling tools for various applications in mold making or CNC milling, such as finishing cutters, roughing cutters, aluminum milling tools and HSS milling tools.
The clear categorization according to material properties - milling tools for steel, stainless steel, titanium, nickel, aluminum, copper, graphite or milling tools for plastic (CFRP) - allows you to make a quick and easy selections. The product range also includes special shapes such as form cutters, deburring cutters and multi-cutters.
Drills: The “Drills” category of the ToolExpert offers you a variety of options to find the perfect drills for your specific requirements. The tool covers all needs, from twist drills, deep hole drills, micro drills to step drills and NC drills. Whether you are machining steel, hardened steel or stainless steel - you will find the right solid carbide drills in ToolExpert. The clear structure and categorization according to material suitability (e.g. drills for steel, aluminum, stainless steel, titanium or CFRP) allow you to quickly select the right drilling tool for your project. Suitable tools such as twist drills and micro drills are also available for special applications, such as drilling in CFRP/metal composites.
Indexable inserts: In the “Indexable inserts” category, ToolExpert offers a comprehensive selection of indexable inserts for various applications. Whether you need round inserts for round insert milling tools, HFC inserts for high-feed milling tools or face inserts for face milling tools, all options are clearly structured in the ToolExpert. You will also find special corner grooving inserts for corner milling tools and corner/groove milling tools.
After selecting the category, the speeds and feeds calculator will guide you to the right cutting data in just a few steps. In the following, we explain step by step how you can determine the cutting data.
Easy access to the cutting data: How to find the right data for your cutting operation
Below we explain how you can determine the right data for your machining project in just a few steps.
The first step is to select the material to be processed. ToolExpert offers you a clearly structured material database, which you can use to search for materials by material number or DIN standard. Alternatively, you can also select directly from categories such as steel, nickel/cobalt/chrome, cast iron/cast steel, aluminum, non-ferrous metals, titanium, graphite, plastics and special materials. The clear subdivision of each category makes it quick and easy for you to find the right material.
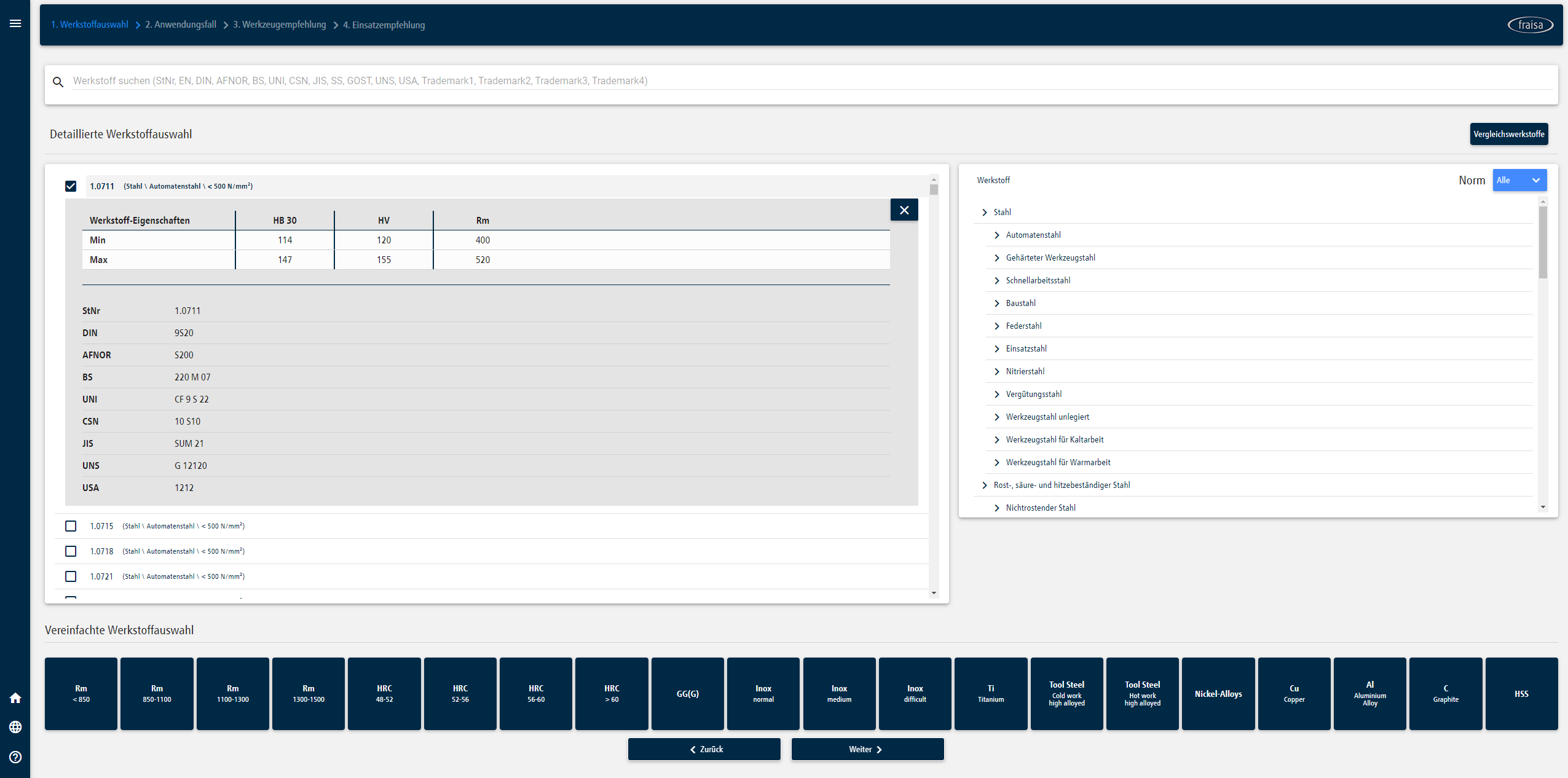
The second step is to select the application. After selecting the material, it is necessary to specify the application. ToolExpert offers you various options, depending on whether it is 2.5D or 3D machining. For 2.5D machining, you can choose between applications such as roughing (High Performance Cutting - HPC milling), roughing (High Dynamic Cutting - trochoidal milling), finishing or plunging (helix and ramps). Options such as High Speed Cutting (HSC milling) and High Feed Cutting (HFC milling) are available for 3D machining. After selecting the application, ToolExpert queries the required tool diameter.
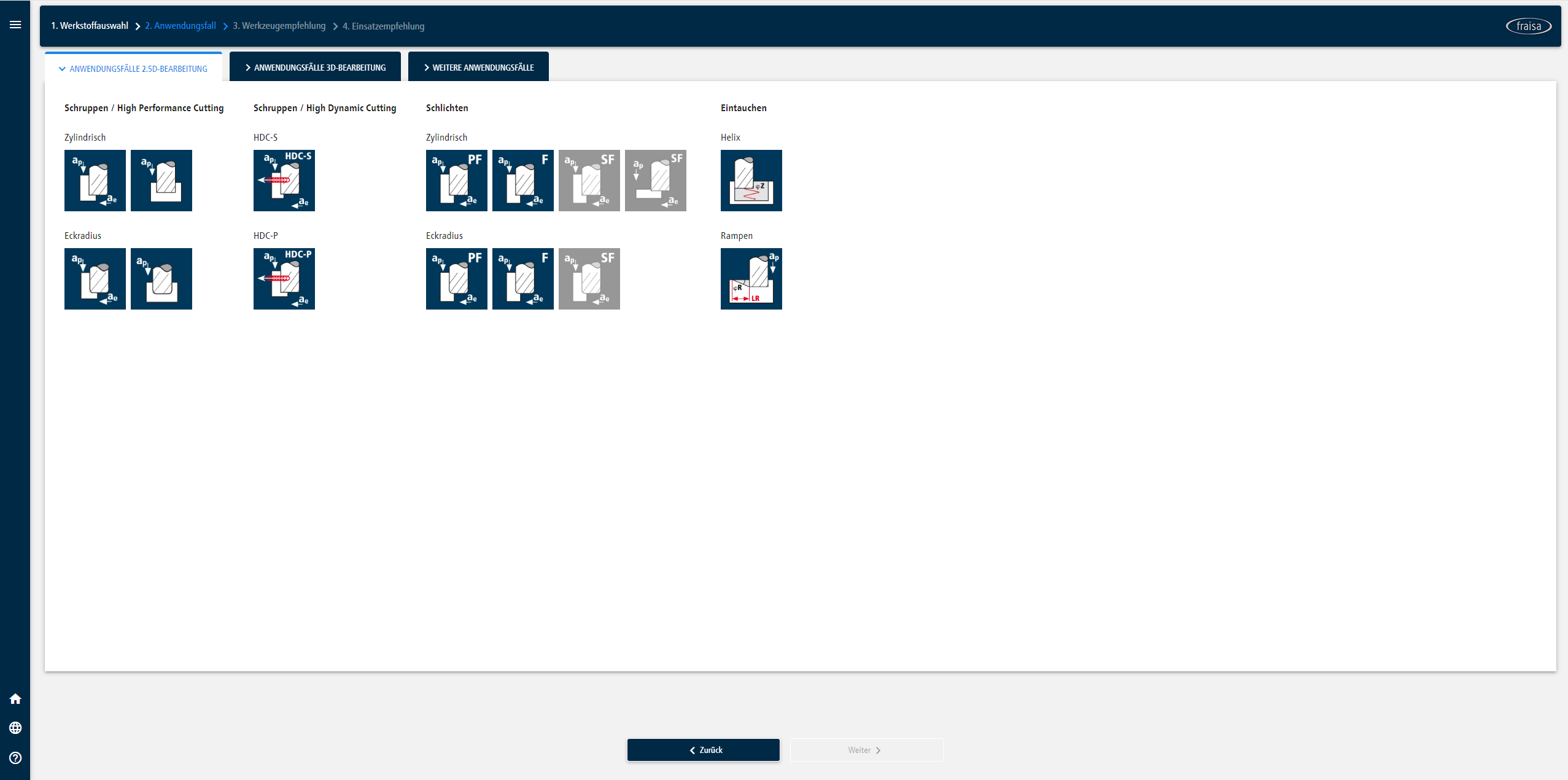
Step 3: Selecting the right tool
Der ToolExpert now generates a list of suitable milling tools based on the previous entries. This overview contains important information such as article number, diameter, shank type, number of teeth/cutting edges and the metal removal rate (Q). Further technical details, such as the coating, feed per tooth (fz), axial (ap) and radial (ae) infeed depth, as well as the cutting speed (vc), can be added as required. It is also indicated whether the tool is suitable for dry or wet machining. The tools are sorted according to FRAISA tool classes (X-Generation, Performance, Favora and HSS), starting with the milling tool with the highest metal removal rate.
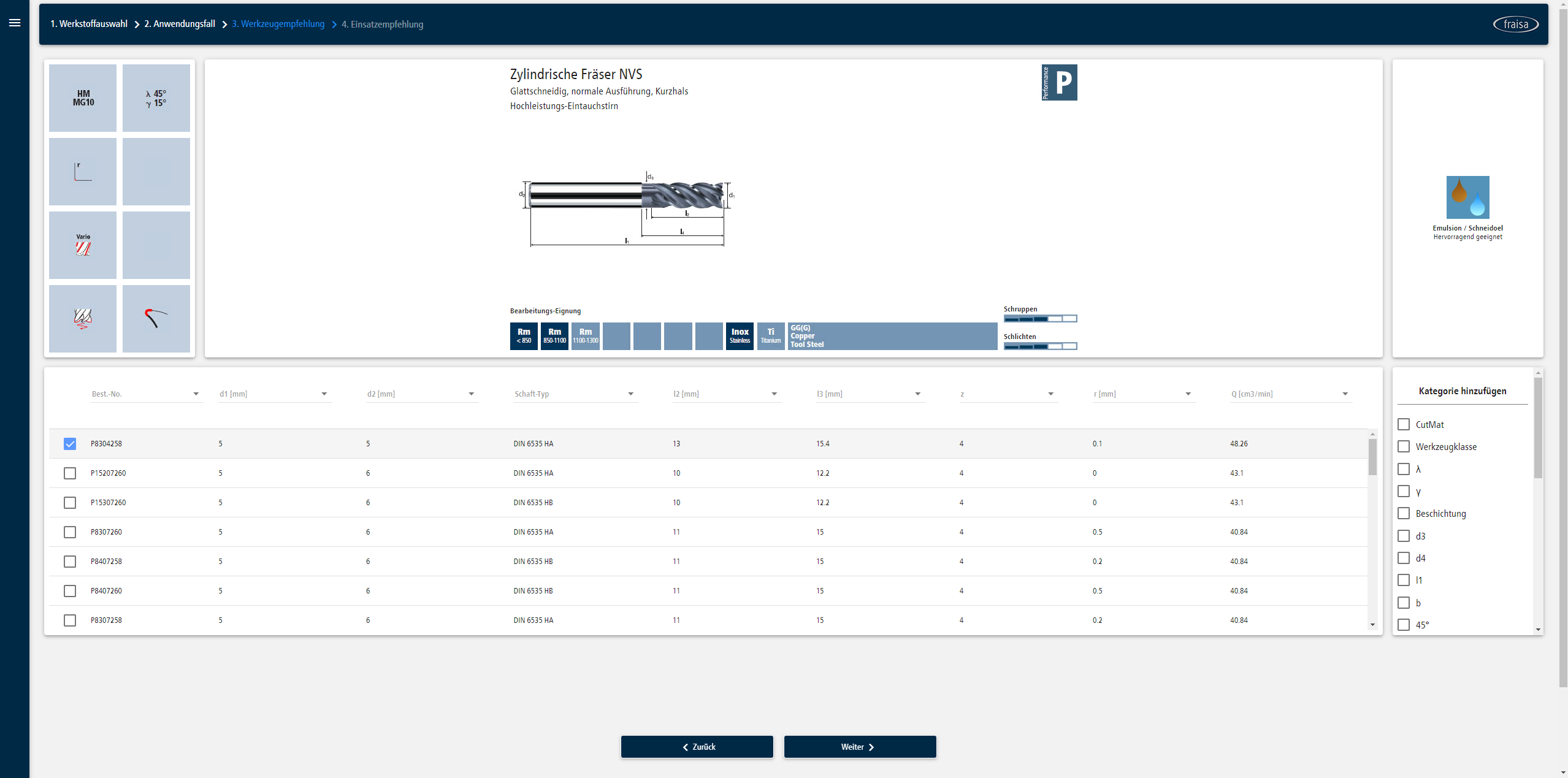
Step 4: Download the data or order the tool
Once you have selected the right tool, you will receive a cutting data recommendation that lists all the relevant parameters for machining. The recommended cutting speed, the feed per tooth, the axial and radial infeed depth, the rotational speed, the speeds and feeds milling and the metal removal rate are also included in the recommendation. are included. When using a ball end mill, the recommendation also contains details such as the angle of attack (β), the effective engagement (deff) and other specific information. The data can be supplemented with further use cases and applications (new material, tool or use case), downloaded as a PDF file or transferred directly to the CAM-System (e.g. with an XML file for hyperMILL®. You also have the option of ordering the tool directly in the webshop and downloading the geometry data of the milling tool as an XML or DXF file. In addition, in some cases you can customize the cutting data and choose between three dynamic ranges for HDC applications (trochoidal milling): low dynamics (10% radial infeed depth of the cutting edge diameter), medium dynamics (7.5% radial infeed depth of the cutting edge diameter) and high dynamics (5% radial infeed depth of the cutting edge diameter).
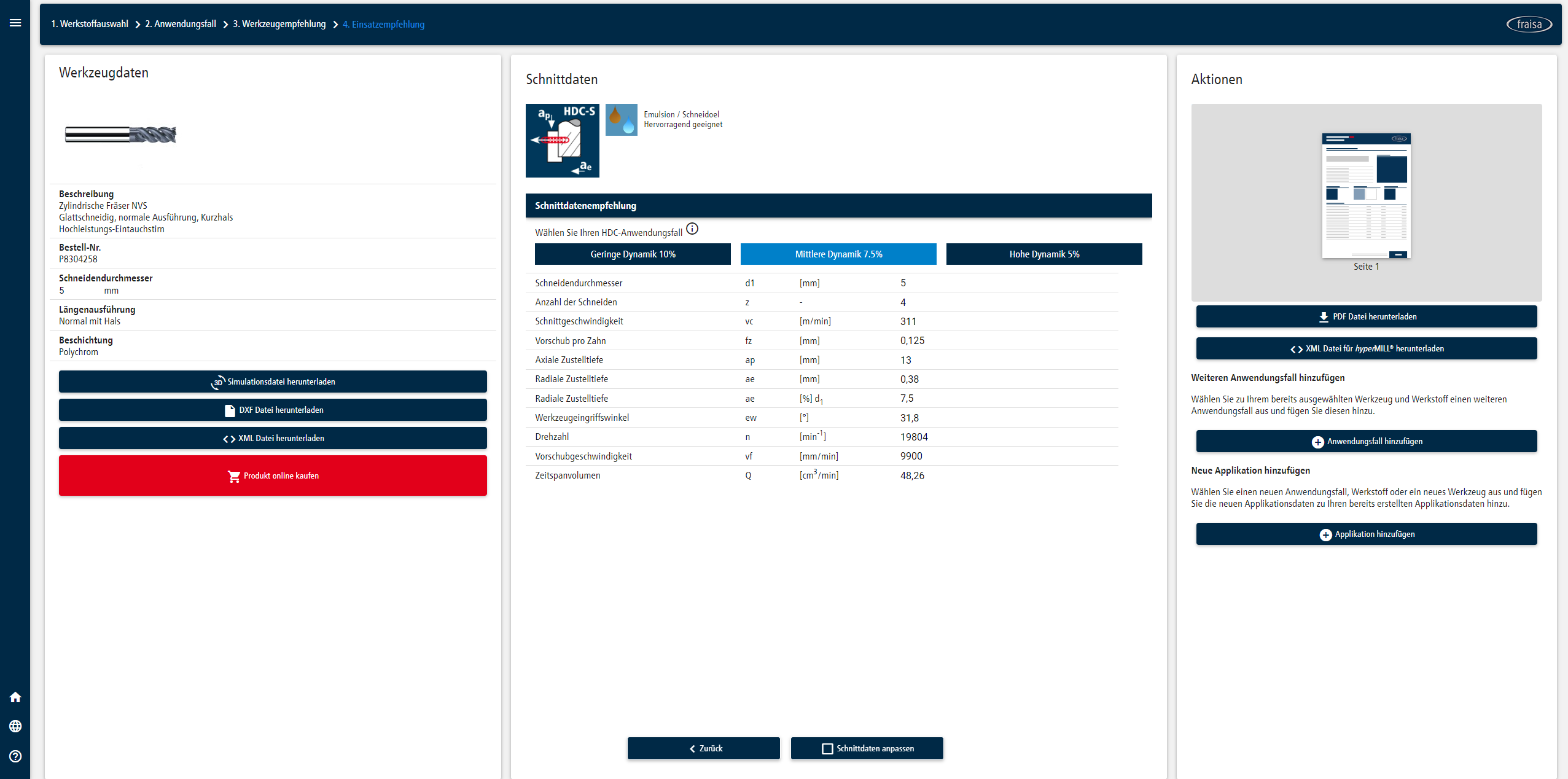
Further options for determining the cutting data
In addition to material selection, ToolExpert offers two other ways to find the right cutting data quickly and efficiently.
Alternatively, the cutting data can also be determined directly via a tool overview. The tool overview is divided according to material suitability, for example into drills for steel, aluminum, stainless steel and titanium as well as drills for CFRP, CFRP/metal composite and NC drills, countersinks.
- Please select a drill bit from the overview first.
- In the second step, please enter the material to be processed or select it from the material database.
- Step 3: Determine the desired drilling strategy.
- Step 4: ToolExpert generates the appropriate cutting data, which can be expanded as required.
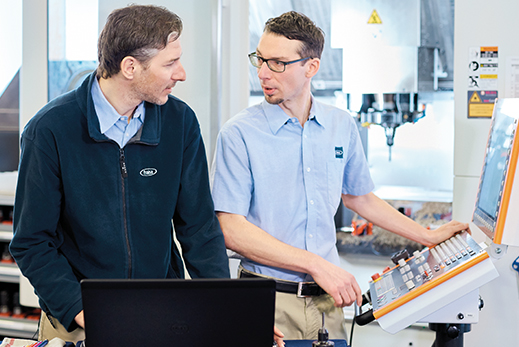
FRAISA's ToolExpert guides you safely and quickly through simple steps to the optimum cutting data for your milling tasks - regardless of whether you are working in the field of CNC milling or conventional milling. ToolExpert can also be used for drilling tasks and machining with indexable inserts. The clear tool selection and precise cutting data recommendations optimize your processes and ensure perfect machining results, no matter what task you have to complete.
Advantages of using the speeds and feeds calculator
FRAISA ToolExpert is an indispensable tool for anyone who needs precise and efficient cutting data for their milling or drilling tasks. Thanks to its user-friendly interface and clearly structured database, the optimum tools and machining strategies can be selected quickly and intuitively.
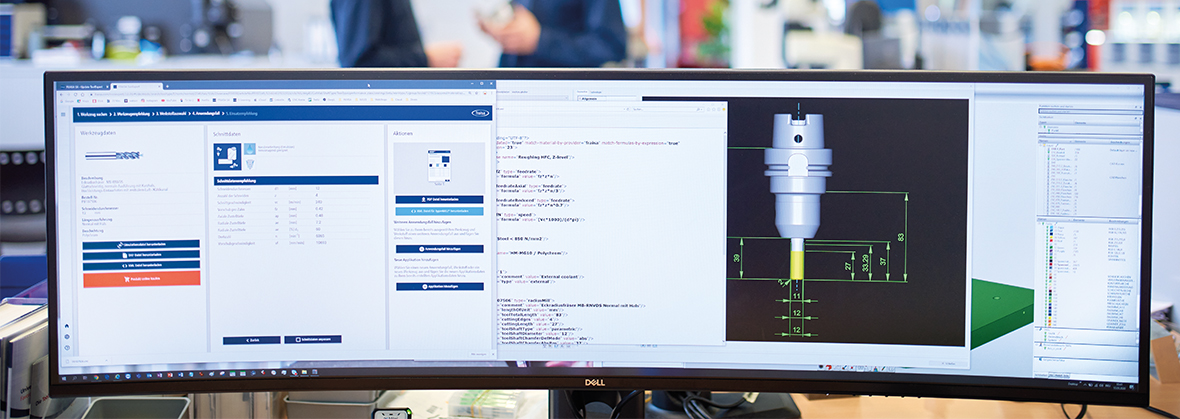
The most important advantages at a glance
Efficient and precise calculation: ToolExpert provides you with precise cutting data for every application. The calculation is based on the factors material, tool and machining strategy.
Versatile application: The speeds and feeds calculator is suitable for a wide range of machining tasks, including CNC milling, conventional milling, drilling as well as machining with indexable inserts.
Easy to use: The clearly structured interface and integrated material database allow you to search for the right cutting parameters quickly and easily, avoiding unnecessary effort.
Flexibility in selection: Various selection options allow you to determine cutting data in different ways. You can choose between selection by material, tool overview or article number, depending on your needs and preferences.
Time saving: The ToolExpert software allows you to find the ideal solution with just a few clicks. This allows you to significantly reduce the time and effort required for selection and calculation.
Webshop, data export and CAM interface integration: The integration with Webshop, data export and CAM interfaces interfaces allows you to easily export data as PDF, DXF, XML, 3D models or order the tool directly in the webshop.
FRAISA ToolExpert is the ideal solution for optimizing your machining processes and achieving the best possible results. The cutting data is developed and validated in the FRAISA ToolSchool, tested and evaluated by our experienced application engineers under real conditions and then made available to you in the ToolExpert. Our speeds and feeds calculator enables precise, efficient production tailored to your individual requirements, even in stand-alone operation.
Integration of ToolExpert into the CAM programming process
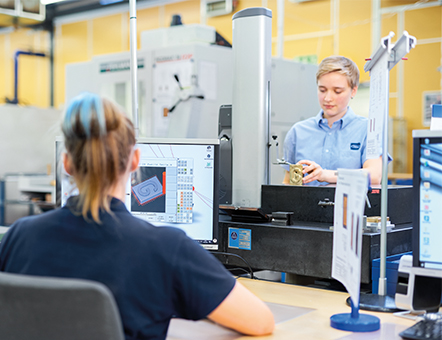
Would you like to transfer your cutting data directly from ToolExpert to your CAM program? Here you will find an overview of CAM programs and how you can connect them to FRAISA ToolExpert.
Do you have any questions about FRAISA ToolExpert®?
Here you will find frequently asked questions and answers:
FRAISA ToolExpert is a speeds and feeds calculator specially developed for FRAISA cutting tools. The tool enables you to quickly and easily determine the ideal cutting parameters for your machining task, even for autonomous production. FRAISA ToolExpert supports you in calculating the rotational speed and feed rate for a wide range of applications with your FRAISA milling tools, drills or indexable inserts. The speeds and feeds calculator takes into account the material to be machined and provides you with the appropriate values for various machining strategies, such as roughing, to achieve the maximum metal removal rate or finishing parameters to achieve particularly good surface finishes.
The milling category provides you with the optimal cutting data for all FRAISA milling tools and various applications such as HPC milling, trochoidal milling or plunge milling. You can easily determine these, regardless of whether you are working in climb milling or up-cut milling.
With the ToolExpert you can:
- Determine RPM for milling
- Calculate the cutting speed
- Use the SFM calculator
- Calculate the metal removal rate
- Determine the axial infeed depth (ap) and radial infeed depth (ae)
- Display the effective pressure angle (deff), rake angle (ß) and plunge angle
- Determine the cutting edge diameter (d1) and number of cutting edges (z)
ToolExpert also determines the optimum drilling parameters for FRAISA drills such as twist drills, deep hole drills, step drills, NC spot drills or countersinks. Here, too, precise values are provided for the rotational speed, cutting speed and speeds and feeds .
With the ToolExpert you can:
- Calculate the rotational speed
- Use the SFM calculator for drilling
- Determine the Speeds and feeds
- Determine the metal removal rate
- Calculate the main machining time
- Determine the maximum and effective drilling depth
FRAISA ToolExpert helps you to find the perfect tool and the best machining strategy for your production - regardless of material and application. This saves you valuable time and optimizes your production processes.
FRAISA ToolExpert is a powerful tool for anyone who needs precise and efficient cutting data for their milling or drilling tasks. The interface is intuitive to use and the material database is comprehensive. This allows you to quickly and easily select the optimal tools and machining strategies for the material in question.
The most important advantages at a glance
- ToolExpert provides precise cutting data for every application, which is also suitable for autonomous operation. The consideration of the material, tool and machining strategy enables a particularly efficient and precise calculation.
- The tool offers a wide range of possible applications: the speeds and feeds calculator is suitable for a wide range of machining tasks, including CNC milling, drilling and machining with indexable inserts.
- Operation is intuitive and uncomplicated. The clear user interface enables quick and easy handling, while the integrated database provides all the important material data. This allows you to select the right cutting parameters quickly and easily. This saves time and effort.
- The selection can be designed according to your individual specifications. ToolExpert offers you various selection options for determining the cutting data. For example, you can search by material, tool type or article number to obtain the results suitable for your individual requirements.
- You have the option of downloading the cutting data recommendation as a PDF, exporting CAD 3D models for your CAM projects as DXF or XML files and ordering the tools directly in the webshop
- FRAISA ToolExpert is therefore the ideal solution for optimizing your machining processes. It supports precise, efficient production tailored to your requirements, leading to the best possible results.
FRAISA ToolExpert supports FRAISA milling tools, drills and indexable inserts as well as their common applications. FRAISA ToolExpert provides precise cutting data for milling (e.g. contour milling, pocket milling or deburring), as well as for drilling, whether core hole, through hole or blind hole. The data is matched to the respective material, tool and selected machining strategy.
CNC milling tools and milling applications:
- Milling tools for steel, stainless steel and nickel: cylindrical end mills, roughing cutters, torus cutters (corner radius cutters), finishing cutters, face finishing cutters, micro milling tools for micro machining
- Milling tools for 3D machining: ball end mills (ball nose end mills), barrel end mills (circular arc end mills, circular segment end mills), torus end mills (corner radius end mills), HFC end mills, high-feed end mills, diamond end mills and CBN end mills
- Milling tools for aluminum and copper: smooth-edged cylindrical end mills, roughing cutters, torus cutters (corner radius cutters), ball nose end mills (ball nose end mills), finishing cutters, micro milling tools
- Milling tools for graphite: micro milling tools (ball nose, corner radius or cylindrical), ball nose end mills, torus end mills (corner radius end mills)
- Milling tools for CFRP: cylindrical end mills Milling tools with special shapes, including form milling tools, deburring cutters, multi-milling tools, roll end milling tools, profile milling tools
The following applications are available for your CNC programming needs, depending on the material and tool to be machined, which can also be combined with each other:
- 2.5D machining: Roughing (HPC milling sideways and grooving), roughing (HDC milling partial cut), swapping (helix and ramps), finishing (pre-finishing and finishing)
- 3D machining: Roughing (plane roughing), finishing (plane finishing), HSC milling (plane roughing, contour-parallel roughing, pre-finishing steep areas, finishing steep areas, ultra-fine finishing steep areas and flat areas, HFC milling (plane roughing), finishing (planes, free-form surfaces, radius areas, flanks, walls and lateral surfaces)
Drills and drilling applications:
- Drills for steel, aluminum, stainless steel and titanium: twist drills, deep hole drills, micro drills, step drills
- NC spot drills, countersinks: NC spot drills (90°, 120° and 144°), countersinks
Indexable inserts and their applications:
- Round indexable insert milling tools: Round insert milling tools
- HFC indexable insert milling tools: High feed milling tools
- Face insert milling tools: 45° face milling tool
- Corner/flute indexable insert milling tools: 90° corner milling tool, 90° flute milling tool
If you know the material number, you can enter it directly in FRAISA ToolExpert To do this, please go to the “Tool selection (Expert)” area and enter the desired material number. The ToolExpert supports a large number of standards, including
- StNr, EN, DIN, AFNOR, BS, UNI, CSN, JIS, SS, GOST, UNS, USA
- Trademarks: trademark1, trademark2, trademark3, trademark4
Alternatively, you can use the detailed material selection to search for and select the material. The clear structure allows you to find the right material based on specific properties and requirements:
- Steel: free-cutting steel, hardened steel, hardened material steel (1. 2379 / K110 / X153CrMoV12, X40Cr14), high-speed steel (HSS), structural steel (S235JR / St37, Hardox, S355J2 / St52), spring steel (51CrV4), case-hardening steel (C15E), nitriding steel (EN 10085, 31CrMo12), quenched and tempered steel (Ck45 / C45E), unalloyed tool steel (C45W), tool steel for cold work (X155CrVMo12-1 / 1 2379 machined / 1 3343 machined), tool steel for hot work (X37CrMoV5-1)
- Rust, acid and heat-resistant steel: stainless steel (X5CrNi18-10, 17-4PH), heat-resistant steel, high-temperature steel (X6NiCrTiMoVB25-15-2) Nickel - cobalt-chromium: nickel, nickel alloys, nickel-iron alloys, nickel and cobalt alloys, cobalt-chromium alloys, nickel-chromium alloys (Inconel 718), high-temperature alloys
- Cast iron / cast steel: conventional cast steel, stainless cast steel, heat-resistant cast steel, gray cast iron, ductile cast iron (GGG-60), vermicular cast iron
- Aluminum: Aluminium (AW-6082), Aluminium Magnesium, Magnesium Legierung
- Non-ferrous metals: copper (E-Cu58), brass (CuZn38Pb2), bronze, Ampco
- Titanium (Grade 5, Ti6Al4V)
- graphite
- Plastics: Thermoplastic (polymethyl methacrylate), thermoset, fiber-reinforced plastic
- Special materials: Tungsten and tungsten alloys, molybdenum, tantalum and niobium, metal matrix composites, precious metals, silicate ceramics, oxide ceramics, medical technology
FRAISA ToolExpert allows you to calculate the cutting data for several materials with just a few clicks. To add another material, please click on the “Add application” button. The ToolExpert automatically determines the appropriate cutting data for each material, so that manual adjustment is not necessary in most cases. In certain cases, however, it is possible to adjust the cutting data yourself if this is necessary due to specific requirements or materials.
The cutting data calculated in FRAISA ToolExpert is extremely precise and enables you to implement your machining processes quickly and reliably. FRAISA invests a considerable proportion of its total development costs in the development and validation of this data. In the FRAISA ToolSchool, applications and materials are extensively tested and evaluated by experienced application engineers under real conditions. The result is proven plug & play solutions that avoid costly experiments in your company and make your CNC programming simple and reliable - even in autonomous production, where the machines run for several hours without human supervision.
The cutting data can be downloaded as a PDF file. You also have the following options for exporting data:
- Tool data as an STP, DXF or XML file
- Cutting data as XML file (for hyperMILL®) in addition to download as PDF file
- Data transfer directly to the CAM program via TopSolid, MDM and Siemens NX
You can start the cutting data calculation with the “Tool selection catalog” option. In the next window, after selecting a use case, you have the option of selecting another use case directly using the “Add use case” button. With the other two options, “Tool selection (expert)” and “Search tool”, you can also select further use cases after selecting the material, the tool and the first use case by using the “Add use case” button.
If you already have a tool for which you would like to determine the appropriate cutting data, you can enter the corresponding article number in the tool search. In the next step, you can select the material and the application.
If you do not yet know which milling tool, drill or indexable insert is suitable for your tasks, you can use the material selection and the desired application to display suitable suggestions for suitable milling tools, drills or indexable inserts. FRAISA ToolExpert then creates a list of suitable tools. It is also possible to order the selected product in the “Application recommendation” area by clicking on it in the webshop.
The order in which the tools are displayed depends on the option selected to determine the cutting data.
If the “Tool selection (expert)” option is selected the tool with the highest metal removal rate (Q) is displayed first (typically all the tools of the X-Generation), followed by all tools in the “Performance” tool class. The milling tools in the Favora and HSS tool classes follow the same principle.
For the other options, the tools from the X-Generation class are also displayed first, with the smallest diameter in first place. The other three tool classes Performance, Favora and HSS follow, sorted by diameter in ascending order.
FRAISA's HDC converter allows you to make the most of the advantages of the high dynamic milling strategy by precisely converting HPC cutting data into HDC cutting data. All you have to do is enter the cutting diameter, the number of cutting edges and the cutting length - ToolExpert does the rest. High Dynamic Cutting (HDC) offers significant advantages over conventional HPC (High Performance Cutting) milling strategies. With HDC milling strategies such as trochoidal milling, cutting conditions such as machining forces and temperature are kept constant during the operation. This results in a significant increase in the metal removal rate, which is often twice as high as with conventional methods. At the same time, tool wear is reduced thanks to stable cutting conditions. This shortens the machining time and significantly increases the service life of the tools. In addition, process reliability is increased, which leads to more efficient and reliable machining processes overall.
You have the option of ordering the tool you have selected directly via the ToolExpert in our webshop. Alternatively, you can also call this up in the PDF file with the cutting data recommendations and order it with a click in the Webshop or contact the Fraisa office to place an order.
The integration of an XML or JSON interface enables the direct import of cutting data into the CAM or TDM system. Compared to manual input, this significantly reduces the time required and susceptibility to errors.
The following CAM interfaces are currently available:
- hyperMILL® from OPEN MIND (XML interface)
- TopSolid (XML interface)
- MDM (JSON interface)
- Siemens (NX Tools)
This link will take you to the partner overview, where you will find further information on the function of the interfaces and their integration: https://www.fraisa.com/fr/en/interface-fraisa-toolexpert/.
On our FRAISA website you will find exciting and informative articles about our speeds and feeds calculator FRAISA ToolExpert:
- Efficient milling and drilling with the FRAISA ToolExpert speeds and feeds calculator
- A brief introduction to the FRAISA ToolExpert speeds and feeds calculator: What can it do?
- The most important functions of the ToolExpert speeds and feeds calculator at a glance
- The user interface of the ToolExpert speeds and feeds calculator: How you can quickly find your way around
- Easy access to cutting data: How to find the right data for your cutting operation
- Advantages of using the speeds and feeds calculator
- Integration of ToolExpert into the CAM programming process
- FAQ
Or send us an e-mail with your questions: